C’est quoi une configuration d’usine en mode Lean?
L’une des clés de réussite de la gestion d’une usine est de disposer d’une configuration efficace. Elle aura un effet direct sur l’ensemble du fonctionnement de votre entreprise, y compris les processus de production, les stocks, l’expédition et l’administration.
Lorsque l’on parle de la configuration de l’usine, les avis divergent toujours sur ce qu’est une “bonne” configuration. Les points de vue varient en fonction du type de configuration que vous souhaitez réaliser.
Chez TXM, nous considérons qu’une configuration d’usine est efficace lorsqu’elle applique les principes du Lean. Comme vous le savez peut-être déjà, le Lean élimine les gaspillages et apporte de la valeur à vos clients en réduisant les coûts, en améliorant la qualité, en réduisant les délais de livraison, en améliorant la sécurité et en renforçant la motivation des équipes.
Les installations en mode Lean créent un flux continu de matériaux et d’informations, minimisant le délai et les efforts de manutention, générant un gain d’espace au sol, réduisant les délais de livraison, augmentant la productivité et la qualité. Si vous concevez ou réaménagez vos ateliers de production avec une configuration en mode Lean, vous obtiendrez une utilisation plus souple et plus efficace de votre espace de travail.
Quelles sont les différences entre une configuration traditionnelle et une configuration d’usine en mode Lean?
Il existe plusieurs facteurs qui différencient une configuration d’usine en mode Lean d’une configuration traditionnelle.
Se baser sur les processus versus se focaliser sur la chaîne de valeur
Une configuration traditionnelle d’usine se focalise davantage sur des ateliers basés sur les processus : Typiquement, les machines de même type sont regroupées ensemble. Une usine traditionnelle de fabrication est divisée en ateliers de découpe, de fabrication, d’usinage et d’assemblage.
La configuration d’une usine en mode Lean se focalise sur la chaîne de valeur, c’est-à-dire toutes les étapes de la fabrication d’un produit allant depuis la commande des matières premières jusqu’à la livraison des produits finis au client. Les configurations en mode Lean combinent les étapes de production avec une orientation produit à travers l’usine, comparée aux regroupements de processus présents dans une configuration traditionnelle. Dans une configuration en mode Lean les processus sont reliés entre eux dans le sens du produit fini. Les besoins en manutention et manipulation qui en résultent sont beaucoup moins importants.
En raison des énormes quantités de stocks entre les processus et des différents accidents causés par les chariots élévateurs, un directeur d’usine a décidé dans le cadre d’un réaménagement de son usine de ne plus avoir de chariots élévateurs dans l’atelier. La nouvelle configuration a permis de réduire considérablement la manutention, les chariots élévateurs ont été supprimés, la taille des lots a été réduite, ce qui a permis de diminuer les stocks d’en-cours et de raccourcir les délais.
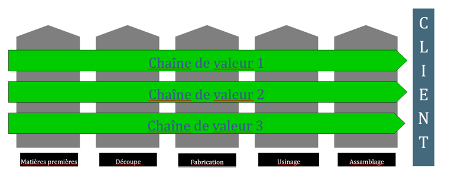
Coût unitaire versus Flexibilité
La plupart des usines que nous visitons possèdent plusieurs grandes machines visant à produire en masse. Pour garantir la qualité et le coût unitaire du produit, cette production en masse a besoin de lots de production très importants, et rencontre des difficultés lorsqu’il s’agit de gérer la diversité dans les commandes.
Les gros équipements peuvent être rentables à l’unité, mais souvent ils entravent les flux de matériaux dans l’usine. Les concepteurs traditionnels de configurations d’usines placent ces grandes machines dans leurs plans sans se soucier des flux ou des interruptions. Ils montrent avec fierté la capacité des lignes de production et le faible coût par unité. Cependant, ils oublient généralement de mentionner que les grosses machines sont généralement coûteuses, qu’elles génèrent un inventaire d’en-cours plus important avant et après la machine, et qu’elles ne sont pas du tout flexibles lorsque la demande n’est pas régulière, ce qui arrive assez souvent.
Au lieu d’utiliser des machines trop grandes, impossibles à déplacer facilement dans des configurations d’usines traditionnelles, les configurations en mode Lean privilégient des équipements plus petits et dédiés à chaque famille de produits. Ainsi, des équipements de taille appropriée sont sélectionnés pour répondre à la demande de la chaîne de valeur, c’est-à-dire aux changements rapides pour des lots de plus petites tailles.
Plus important encore, ces petits équipements sont faciles à installer, à déplacer et plus flexibles aux fluctuations des quantités demandées par le client. Certaines cellules de production ont même des équipements sur roulettes pour faciliter le déplacement et respecter les délais des clients. Les configurations en mode Lean utilisent des équipements de petite taille pour rendre le flux vers les clients plus rapide et plus flexible, ce qui aide les fabricants à être plus agiles face à la demande.
Design versus Contrôles visuels
Les usines sont censées être fonctionnelles. Parfois, certaines considérations esthétiques peuvent l’emporter sur le bon sens. Nous avons vu des usines avec un très beau design intérieur, avec de grands espaces entre les lignes ou les machines, ou même des fontaines, des arbres, des tables et des chaises entre les machines. Mais, un espace vide est rapidement occupé par un excès de matières ou un stock d’en-cours excédentaire.
Et qui dit grands espaces, dit mouvements inutiles de produits ou de personnes. De plus, le personnel ne s’assoit jamais dans « le jardin intérieur » de l’usine qui s’avère être un obstacle à contourner dans le transport de produits vers le processus suivant. Ainsi, lorsque vous créez la configuration d’une usine, oubliez la beauté esthétique du lieu et concentrez-vous sur sa fonctionnalité. Chez TXM, nous pensons qu’un atelier de production bien conçu, qui « roule » et avec un bon takt time est une sorte de beauté en soi !
Les configurations d’usines en mode Lean disposent généralement de peu de place entre les machines, ce qui empêche l’accumulation d’en-cours intermédiaires et réduit les mouvements inutiles des hommes et matériaux. En générant moins de gaspillages, les excès de produits seront réduits, tout comme la surproduction, les mouvements et les transports inutiles.
De plus, lorsqu’il y a du gaspillage celui-ci devient visible. La configuration des installations en mode Lean permet de rationaliser les flux de personnes, de matériel, de produits et d’informations, et d’utiliser des contrôles visuels pour rendre visibles les obstacles et les interruptions des flux.
Les usines configurées en mode Lean utilisent des contrôles visuels pour une meilleure communication et mettent en place des standards visuels. Des marquages au sol adhésifs sont utilisés au lieu de la peinture appliquée sur le sol de l’usine, ce qui rend la communication des changements d’aménagement plus facile et moins coûteuse.
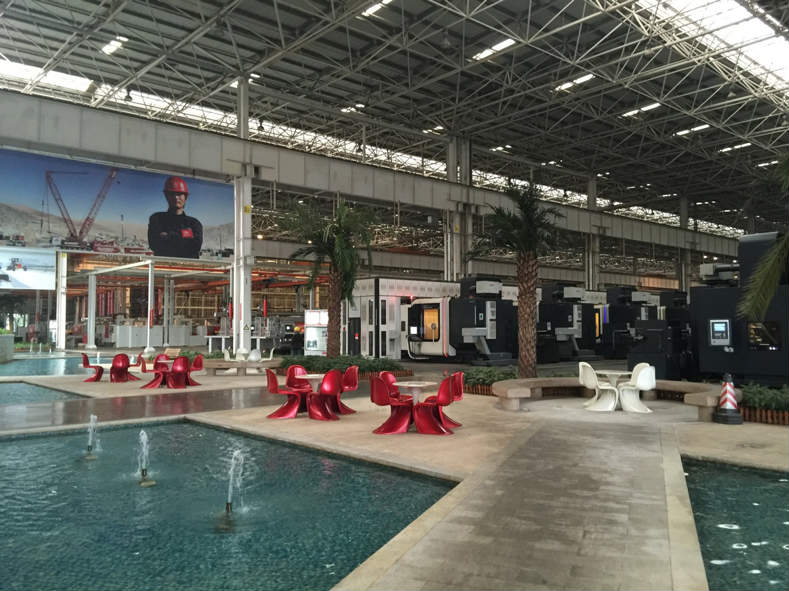
Qu’est-ce qu’une une bonne configuration d’usine en mode Lean?
Alors comment savoir si votre installation a une implantation correcte ? Voici cinq critères qui vous permettent de vérifier si votre configuration est vraiment Lean.
Connexion avec la demande Client
Les usines en mode Lean permettent de livrer aux clients des produits sans défauts et dans les délais requis. L’un des facteurs clés d’une installation en mode Lean est que les flux de valeur sont reliés à la commande du client et permettent de répondre rapidement à sa demande. Autrement dit, ce sont les commandes des clients qui déterminent l’activité, et non les besoins internes pour rentabiliser les machines. Les opérateurs de chaque processus et leurs chefs d’équipe comprennent ces concepts et sont formés pour adapter la production à la demande.
La configuration d’une usine en mode Lean permet non seulement de relier l’ensemble de la chaîne de valeur aux clients externes, mais aussi de relier les processus aux clients internes. Au lieu de recourir à des silos de traitement dans la production traditionnelle par lots, l’implantation en mode Lean rapproche les machines, permet de produire des séries plus petites ou même de produire en flux unitaire. Elle permet de signaler des défauts de manière très rapide et donc de fabriquer moins de produits défectueux. Le fait de relier les processus des fournisseurs, les processus des clients et la communication facilite considérablement le processus d’amélioration continue.
Flux
L’élément essentiel d’une configuration d’une usine en mode Lean est le flux. Dans un autre article de TXM, nous avons évoqué les “7 flux à prendre en compte lors du design de la configuration de votre usine”. Il s’agit des flux de matières premières, d’en-cours, de produits finis, de consommables, de mouvements de personnes, de déchets et d’informations. Les longues distances, les longs délais d’installation, les grosses machines pour les productions de gros lots, une mauvaise maintenance et les goulots d’étranglement des processus constituent des obstacles classiques aux flux.
Une bonne implantation permettra à ces flux de circuler efficacement dans tous les processus. Nous utilisons le terme « flux de valeur » pour décrire les activités à valeur ajoutée qui y sont rattachées. Nous voulons le bon déroulement de ces processus, sans blocages de flux de matériaux, ni d’informations ni de personnes. Les flux interrompus dans l’usine doivent être évités. S’il y a des flux bloqués, ils doivent être facilement détectés et éliminés. Par exemple, des machines faciles à installer et à entretenir peuvent être placées ensemble dans la même chaîne de valeur avec un temps de cycle équilibré qui rationalise le processus autant que possible.
Flexibilité
Une nouvelle implantation vous permettra d’envisager une série de changements : une plus rapide expansion due à l’augmentation de la demande, au lancement de nouveaux produits, aux changements de méthodes ou d’équipements, ou pour répondre aux exigences en matière de sécurité et d’environnement. Il est donc essentiel de concevoir une configuration qui soit suffisamment flexible pour s’adapter aux changements futurs. Et il est donc préférable d’utiliser des équipements petits et faciles à déplacer. Il est tout aussi conseillé de préserver une « réserve d’espace » pour un éventuel agrandissement ou la fabrication de nouveaux produits, plutôt que de céder de l’espace aux en-cours.
Moins de gaspillage
Une mauvaise implantation embarque fatalement des inefficacités qui seront ressenties au quotidien. Comme nous l’avons vu précédemment, la production de masse traditionnelle entraîne de longs délais de production. La surproduction de gros lots remplira l’espace vide avec des en-cours importants. Ces stocks entraîneront par la suite une augmentation du transport des matières, des mouvements du personnel et du surprocessing. La surproduction mettra en attente les autres produits, et on verra apparaître des défauts car ceux-ci sont souvent découverts seulement après la fabrication d’un lot de grande taille. Le travail en masse provoque une infra utilisation des compétences des personnes. Voilà les huit gaspillages du Lean réunis !
Les configurations en mode Lean génèrent moins de gaspillages et favorisent l’amélioration continue. Le flux continu permet une production constante, avec moins de stocks et de temps d’attente. Les espaces plus petits entre les machines réduisent non seulement les mouvements des opérateurs, mais rendent également difficile la surproduction. La place pour les en-cours de production est dimensionnée avec le même niveau d’exigence que l’implantation des machines elles-mêmes, donc vous êtes obligé de corriger les causes qui génèrent les en-cours excessifs.
Un nouveau standard
Une configuration en mode Lean ne doit pas être élaborée par une seule partie prenante. Au contraire, cela doit être le fruit d’un effort de collaboration de la part d’un ensemble de parties prenantes de l’entreprise.
L’intégration des différents points de vue dans la conception de la configuration de l’usine et leur contribution au développement des plans d’aménagement est essentielle pour que la transformation de l’usine soit un succès. Cependant, mettre l’accent sur l’expérience de l’utilisateur n’est généralement pas suffisant pour développer une configuration réussie.
Elle peut simplement conduire à un nouveau plan d’aménagement similaire à l’actuel, avec autant de gaspillages. C’est pourquoi nous organisons généralement un workshop de cartographie de la chaîne de valeur avant la mise en place de la nouvelle configuration de votre usine et nous nous mettons d’accord à partir de quelle chaîne de valeur nous devons travailler.
Une bonne implantation doit aboutir à la mise en place d’un nouveau standard. Une étape clé est la formation de toutes les personnes concernées aux compétences basiques en matière de Lean. Certains outils Lean de base, tels que le travail standardisé, les 5S, le flux continu et le changement rapide sont pertinents. Sans ces compétences, les opérateurs auront du mal à abandonner les anciennes habitudes et à trouver leur place dans la nouvelle configuration.
Pourquoi est-il important d’avoir une configuration d’usine en mode Lean?
La transformation d’une usine avec une configuration en mode Lean peut être éprouvante, mais vous serez largement récompensé par la suite. Par rapport à une implantation traditionnelle, une usine bien conçue peut vous apporter toute une série d’avantages:
- Elle minimise la distance et le temps de déplacement des matériaux;
- Elle permet de gagner de l’espace au sol;
- Elle augmentera la qualité des produits en réduisant les défauts des gros lots;
- Elle évite les stocks excessifs d’en-cours;
- Elle réduira les délais de livraison;
- Elle simplifiera les flux de personnes, des matériaux et d’informations et rendra les gaspillages plus visibles;
- Elle réduira les investissements et les coûts de production pour l’ensemble de la chaîne de valeur;
- Elle établira un nouveau standard qui sera le garant du résultat à atteindre;
- Elle aura un effet positif sur la sécurité et le mental des travailleurs et favorisera l’amélioration continue;
- Elle rendra les futurs aménagements plus flexibles et plus faciles.
N’oubliez pas qu’il n’y a pas une configuration d’usine parfaite ; vous aurez toujours une marge de manœuvre pour poursuivre l’amélioration continue.