Cinq conseils Lean Manufacturing pour une amélioration de la qualité
Depuis le début il y a bientôt 40 ans du « Mouvement pour la qualité » dirigé par des personnes comme W. Edwards Deming, notre perception et compréhension de la qualité se sont énormément améliorées, tout comme les attentes des clients en matière de qualité. Cependant, nos consultants TXM trouvent encore des entreprises qui ont du mal à relever le défi de la qualité du premier coup et de manière systématique. Quelles sont donc les meilleures techniques et pratiques que nous avons découvertes pour améliorer la qualité des produits et des services ?
1. Être rigoureux sur le principe de la « qualité avant tout »
Nous le disons tous, « La qualité passe en premier », mais le pensons-nous vraiment ? Allons-nous SYSTEMATIQUEMENT arrêter la production pour éviter davantage de défauts, sommes-nous TOUJOURS sûrs que le produit que nous envoyons à un client répond à ses exigences ?
Le concept de qualité du premier coup ou de qualité à la source est simple. En d’autres termes, chaque processus est responsable de sa propre qualité et ne transmettra pas les défauts au processus suivant ou au client. Mais il est bien plus difficile d’atteindre cet objectif et d’après notre expérience, l’une des raisons principales est que les managers envoient des messages contradictoires.
En effet, lorsque le produit doit être mis au rebut, ou retravaillé, ou qu’il est renvoyé par le client, les managers se sentent frustrés et sermonnent, voire sanctionnent les opérateurs pour leurs « erreurs ». Toutefois, lorsque la pression est exercée pour atteindre les objectifs de vente ou de production, ou lorsque l’usine a pris du retard, ils feront pression sur ces mêmes opérateurs pour qu’ils fassent fonctionner les machines qui ne sont pas tout à fait réglées correctement, leurs diront de « lancer la production et nous les règlerons à la fin » ou autoriseront un « un dépassement des limites autorisées » lorsque la qualité déroge aux spécifications.
Les opérateurs et les équipes savent très bien détecter ce genre d’hypocrisie et l’interpréteront comme un signal clair : « la direction ne prend pas la qualité au sérieux, alors pourquoi le ferais-je ». Et ils auraient raison. Ce n’est que lorsque vous serez cohérent à 100% en tant que manager et prêt à stopper le processus pour atteindre la qualité que vos équipes pourront constater que vous êtes réellement sérieux et donc suivre votre exemple.
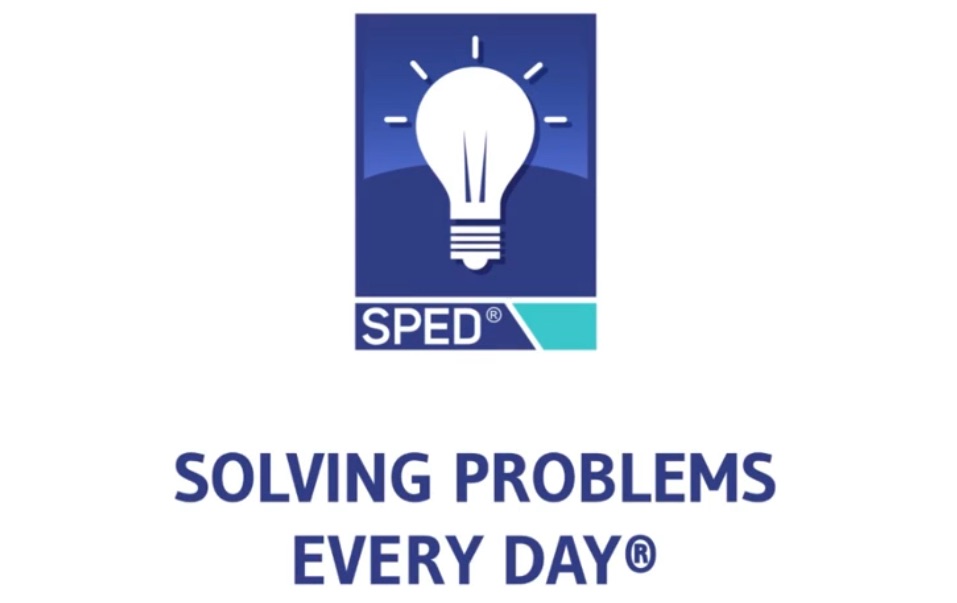
2. Evitez la mise en place d’une inspection à 100%
Si nous voulons vraiment offrir de la qualité au client, nous contrôlerons 100 % des marchandises, n’est-ce pas ? … FAUX !
Si nous voulons vraiment offrir de la qualité au client, nous ferons tout ce qui est en notre pouvoir pour éviter que les défauts ne soient générés en amont.
Lorsqu’un processus est incontrôlable (incapacité d’obtenir une qualité constante selon les spécifications), nous devons alors inspecter les produits pour tenter d’empêcher que les produits défectueux n’arrivent jusqu’au client. Parfois, cette inspection est obligatoire (comme dans l’aérospatiale ou les produits pharmaceutiques) ou les conséquences d’un défaut sont si importantes que l’inspection est tout simplement logique (par exemple, les implants médicaux). Toutefois, cette inspection doit être considérée comme la toute dernière solution et on ne devrait, dans des conditions normales, trouver aucun défaut (car ils seront éliminés en amont).
Malheureusement, nous constatons souvent (surtout en Asie) que l’inspection à 100 % est considérée comme un moyen d’atteindre la qualité, mais cela ne fonctionne pas pour un certain nombre de raisons. Premièrement, aucun inspecteur ou système d’inspection n’est infaillible. Si vous avez des défauts, vous pouvez être sûr que certains parviennent au client, malgré votre inspection.
Deuxièmement, l’inspection agit comme une » protection » qui couvre souvent un manque d’entretien, une mauvaise configuration des machines, une formation insuffisante des opérateurs ou des raccourcis de processus. Les personnes en amont du processus savent qu’elles peuvent « s’en tirer » car les inspecteurs « attraperont le problème » avant qu’il n’atteigne le client.
Troisièmement, l’inspection est très coûteuse. Ajoutez le coût des salaires des inspecteurs au coût de la production qu’ils rebutent, à la capacité de production gaspillée (d’abord la fabrication puis le retraitement du produit défectueux), au coût du transport et du stockage des produits défectueux dans l’usine et aux retards de livraison, et vous constaterez rapidement qu’un niveau relativement faible de défauts peut représenter une très grande partie de votre coût de fabrication.
Par conséquent, le but de l’inspection (si vous en avez une) est de trouver et d’éliminer les sources des défauts :
• Pas d’inspection sans registre
• Pas de registre sans analyse
• Pas d’analyse sans action
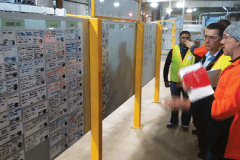
3. SPED
Nous détestons tous avoir des problèmes et nous souhaitons tous que les choses se fassent « en douceur ». Cependant, un fonctionnement « sans heurts » en production signifie généralement que nous n’observons pas les problèmes quotidiens qui affectent la capacité de nos équipes à atteindre la qualité.
Les coachs japonais qui ont formé une grande partie de l’équipe TXM disaient » pas de problèmes, c’est un problème « , ce qui signifie que nous ne remettons pas en cause le standard actuel et que nous n’essayons pas de nous améliorer. Nos commentaires précédents sur les problèmes de dissimulation des inspections en sont un bon exemple.
Lorsque quelque chose ne fonctionne pas, nous devons saisir cette occasion pour trouver et éliminer la cause véritable du problème. Nous pensons que la résolution de problèmes devrait faire partie de la réunion quotidienne sur la zone de travail de chaque équipe dans chaque site de production ; de plus chacun devrait être formé à utiliser ou à participer à l’utilisation de techniques simples de résolution de problèmes telles que les « 5 pourquoi » ou le « diagramme de cause à effet ».
Nous recommandons l’utilisation de fiches de problèmes magnétiques pour résoudre les problèmes quotidiens et pour les problèmes plus complexes, nous suggérons plutôt de recourir à la l’affiche de problèmes en A3 ou à l’approche 8D. L’utilisation d’outils statistiques complexes tels que la mise en place des expérimentations ou des éléments d’analyse des variations est rarement nécessaire car la plupart des problèmes peuvent être résolus à l’aide d’outils très simples que tout le monde peut comprendre. Pour en savoir plus sur l’outil TXM Solving Problems Every Day (SPED), vous pouvez consulter notre page sur la résolution de problèmes en matière de Lean.
4. Le travail standardisé
« Si vous n’avez pas de standard, comment pouvez-vous vous améliorer ». Le travail standardisé est l’élément le plus fondamental d’un système de production Lean. La première « règle » du Lean est que « tout le travail est standardisé en termes de timing, de contenu, de séquence et de résultat ».
Cela signifie que tout le monde fait le même travail de la même manière, avec les mêmes étapes, dans le même ordre et devrait obtenir le même résultat dans le même délai. Le travail standard ne consiste pas à rédiger une procédure opérationnelle standard, mais à engager une équipe d’employés dans une discussion sur la manière dont le travail est réellement effectué, à décomposer les étapes et à convenir de la meilleure méthode.
Cela devient alors la référence, donc le standard, et tous les membres de l’équipe s’engagent à respecter ce standard à moins que l’équipe ne trouve et ne convienne d’une meilleure manière de procéder. Cela semble très simple et logique. Si vous faites les choses de la même manière à chaque fois, si les opérateurs sont tous formés à la même méthode, alors vous devriez obtenir le même résultat.
Lorsque quelque chose ne va pas, la première question est « quelle est le standard ? » et ensuite « l’avons-nous suivi ? ». Nous pouvons alors rapidement voir si le problème a été causé par un écart par rapport au standard (auquel cas nous devons en trouver la raison) ou par une autre cause (comme un défaut de qualité du matériel). Le travail standard ne se limite pas aux tâches liées à la production, mais peut s’appliquer à presque toutes les activités de l’entreprise.
5. Mise en place du système Andon
Les systèmes Andon sont de simples systèmes d’alertes conçus pour permettre à un opérateur de signaler rapidement qu’il ou elle a un problème. L’opérateur tire un cordon ou pousse un bouton qui déclenche une alarme visible et/ou audible.
Le chef d’équipe doit alors répondre à l’opérateur pour l’aider à résoudre le problème. Le problème s’aggrave davantage si le chef d’équipe ne peut le résoudre et la production s’arrête entre-temps. Il s’agit là encore d’un outil très simple mais incroyablement puissant.
Il renforce l’idée chez l’opérateur qu’il ne doit pas transmettre le défaut de qualité au poste à la station de travail suivante et lui permet d’arrêter la ligne et de donner l’alerte en cas de problème. Il permet également de réorienter rapidement les priorités de l’organisation, en focalisant le responsable sur le soutien à l’opérateur pour obtenir un résultat de qualité.
La qualité est l’un des principaux thèmes du blog TXM. Si vous souhaitez en savoir plus, consultez nos autres articles ou parlez à l’un de nos consultants.