Lors de la conception d’une configuration d’usine en mode Lean, beaucoup de personnes partent du principe que la configuration doit être en « U ». Cependant, la solution qui vous convient le mieux dépend de votre process et de vos besoins spécifiques. Voici les principaux exemples de configuration d’usine en mode Lean :
Configuration en forme de “S”
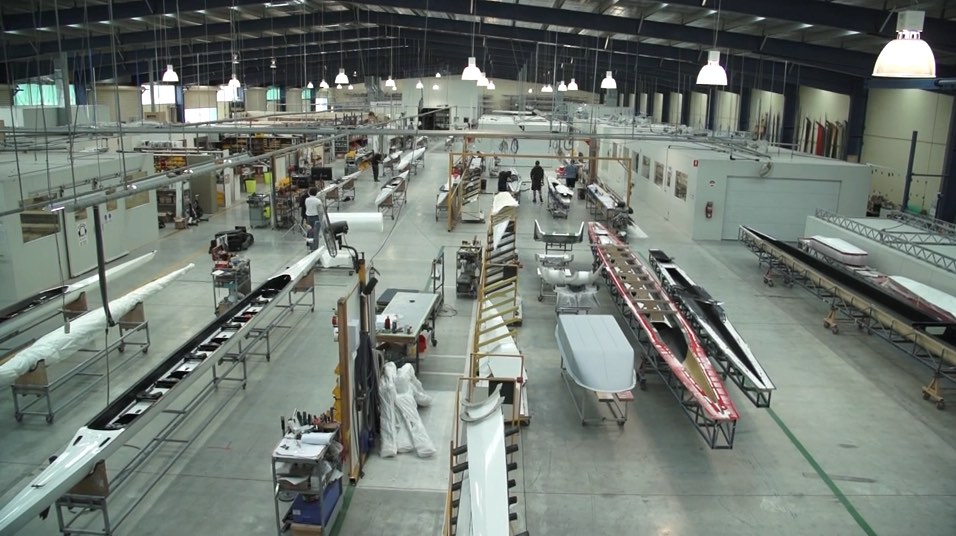
Avec cette configuration, le flux se replie sur lui-même en forme de « S ». Cette configuration est utile lorsque le processus comporte de nombreuses opérations et qu’il n’est pas possible de déplacer ces opérations dans des sous-cellules d’assemblage.
Cette configuration utilise efficacement l’espace mais présente l’inconvénient que les extrémités du « S » peuvent être fermées, ce qui entraîne de plus longs temps de déplacement pour la manipulation des produits.
Un très bon exemple de configuration d’usine en mode Lean utilisant une implantation en « S » est celle que TXM a développée pour le constructeur de bateaux à rames Sykes Racing. Il s’agissait d’un produit physiquement long (jusqu’à 18 mètres) et le processus de production comportait de nombreuses étapes. L’un des grands avantages du « S » était de permettre une bonne utilisation des « retours » du « S ».
Le premier retour permettait le durcissement du matériel composite et un petit tampon stock (FIFO) entre les processus de stratification et d’assemblage. Le deuxième retour permettait de ramener les moules de composite à leur point de départ dans le dépôt de moules, minimisant ainsi le transport de moules vides (et les dommages potentiels).
Configuration en forme de “U”
Dans cette configuration, les matières premières entrent d’un côté du « U » et le produit circule autour du « U » (généralement dans le sens inverse des aiguilles d’une montre) jusqu’à ce qu’il atteigne l’autre extrémité du « U » où il est ramassé. Les avantages de cet exemple de configuration en mode Lean sont :
- Le rapprochement de la réception et de l’expédition des pièces font en sorte que l’opérateur puisse déposer les matières premières et récupérer les produits finis au cours du même trajet ;
- Faciliter les mouvements par l’extérieur des containers de pièces en cours de fabrication, afin que les pièces complètes puissent être déposées depuis l’extérieur du « U » et ramassées depuis l’intérieur ;
- Diminuer l’espace nécessaire pour l’en-cours ;
- Faciliter la supervision et le contrôle visuel des opérations ;
- Augmenter les capacités des opérateurs à travailler sur plusieurs machines ou postes de travail. Cela est particulièrement utile si vous devez augmenter ou diminuer la production.
- Faciliter la mise en œuvre du travail en équipe puisque les membres d’une équipe travaillent en étroite collaboration.
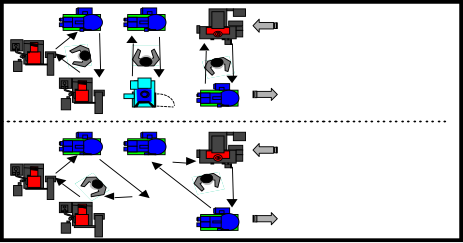
Les bénéfices de la cellule en forme de U sont réduits lorsque de gros équipements ou de multiples processus sont utilisés.
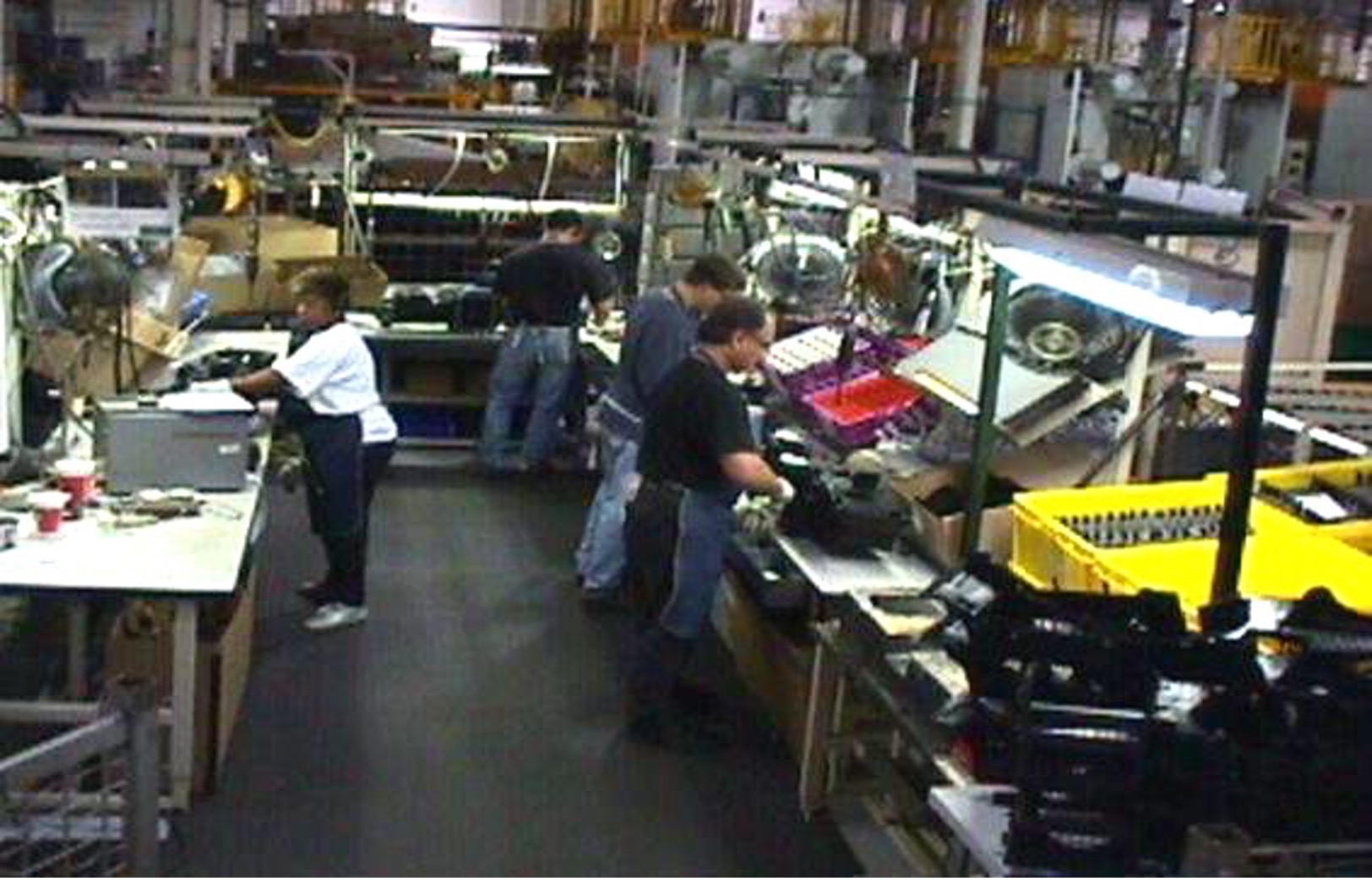
Configuration en forme de “L”
Une configuration en L est utilisée lorsque le flux inter-cellule se fait autour d’un angle. Il s’agit généralement de la disposition la moins efficace en termes d’espace, car il est difficile d’utiliser l’espace situé à l’intérieur du L.
De plus, les allées de circulation des matériaux à l’extérieur du « L » sont souvent longues. Le produit est réceptionné puis expédié dans les coins deux opposés du L. Cependant parfois, comme le montre la photo, une configuration en L est la seule option possible ; elle peut parfois être » placée » le long de l’extérieur d’une cellule en U pour prolonger le flux.
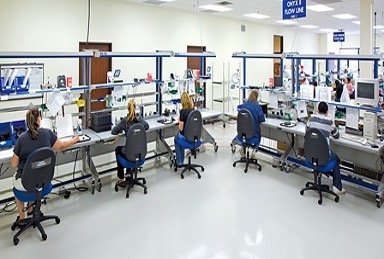
Configuration en forme de “I”
Le dernier exemple de configuration d’usine en mode Lean que nous vous présentons est également le plus courant, à savoir la configuration en « I ». Elle est idéale pour les process comportant un petit nombre d’étapes. Le flux se fait en ligne droite, ainsi les matières premières entrent à une extrémité du « I » et les produits finis sortent à l’autre extrémité.
Souvent, les configurations en « I » sont utilisées pour l’assemblage final et sont alimentées par des cellules de sous-assemblage. Cela permet souvent d’obtenir des délais très courts et de petites emprises au sol. Souvent, plusieurs configurations en « I » sont disposées en parallèle pour différents produits ou alimentent un flux central dans une configuration en « arête de poisson ».
Un excellent exemple de configuration en « I » est la configuration que nous avons développée pour Varian Inc. pour la fabrication d’équipements de spectroscopie d’émission. Cette configuration comprenait plusieurs sous-cellules en forme de « U » et de « I » qui alimentaient directement une courte configuration en « I » pour l’assemblage final.
Découvrez l’exemple de la configuration en mode Lean de Varian.
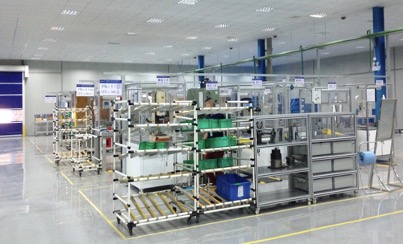
TXM peut vous aider avec l’aménagement de votre usine
Le processus de développement d’aménagement d’usine Lean de TXM fournit la concentration dont vous avez besoin pour que votre équipe travaille ensemble tout au long de cette période difficile. Il est basé sur la compréhension de votre entreprise et la production de flux en utilisant l’approche Value Stream Mapping. À partir de là, des conceptions de cellule détaillées peuvent être déterminées, en tenant compte des sept flux, comme indiqué ci-dessus, ainsi que de la charge de travail de la cellule pour optimiser la disposition de cette gamme de produits.
Ces dispositions de cellules sont ensuite examinées dans le contexte de l’usine pour déterminer la meilleure disposition avec l’équipement et les installations dont vous disposez. Ensuite, l’équipe TXM le fera encore et encore jusqu’à ce que nous ayons couvert plusieurs options. Cela donne à votre équipe l’opportunité d’essayer différentes options et mises en page, en notant les avantages et les problèmes de chaque mise en page et finalement d’arriver à une mise en page convenue qui répond à la plupart des critères tout en comprenant quand des compromis peuvent avoir été faits.
Le meilleur moment pour améliorer l’agencement de votre usine est avant de déménager dans un nouveau bâtiment – faire l’effort de développer un bon agencement d’usine avant de déménager vous fera économiser de l’argent, du temps et le stress de vous tromper !