La fabrication Lean et ses outils ont évolué depuis leurs débuts chez Toyota vers un système que les acteurs industriels utilisent dans le monde entier. La fabrication Lean a généré un certain nombre d’outils et de systèmes standard que l’on peut utiliser à tous les niveaux des entreprises et industries sans grandes modifications. Nous allons étudier ci-dessous les divers outils qui sont à votre disposition.
Les Systèmes 5S
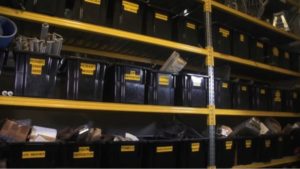
Les 5S est un outil d’organisation du poste de travail qui standardise ainsi un processus:
- Tri sélectif : ne laisser que ce qui est nécessaire pour l’opération
- Mise en ordre : organiser les choses selon vos besoins
- Brillance + Contrôle : garder les choses simples et nettes
- Standardisation : rédiger les normes et les partager.
- Maintien : Contrôler, inspecter et améliorer les normes en vigueur. Répéter.
Les plans A3
Un plan A3 est un simple plan d’activités ou de projets rédigé sur une feuille de papier A3.
Les plans A3 sont utilisés pour résumer et expliquer la stratégie, présenter des projets et résoudre des problèmes. En limitant le format à une seule page A3 et en appliquant des règles autour d’un schéma, les plans A3 garantissent que l’information essentielle sera communiquée de façon claire et concise.
Les indicateurs lumineux Andon
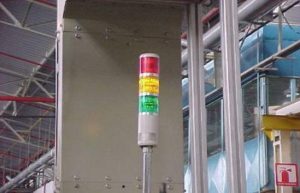
Il s’agit d’un système qui fournit une notification d’une anomalie : c’est un outil typiquement axé autour des superviseurs, de la maintenance et des opérateurs. Il est activé lorsqu’un problème est détecté pendant un processus : un membre de l’équipe a la possibilité d’avertir immédiatement d’un dysfonctionnement de telle manière que l’on peut réagir et affecter du personnel à cette tâche dans un lapse de temps déterminé.
Dans l’industrie, ce dispositif permet à un opérateur d’arrêter la production quand un problème est détecté et de solliciter une assistance. Cela peut aussi s’étendre à une activité de bureau. Dans ce cas, activer une alerte Andon signifie que le processus ne pourra passer à l’étape suivante qu’une fois le problème traité.
Le dispositif Andon peut être déclenché automatiquement ou manuellement en appuyant sur un bouton. Parmi les motifs le plus courants pour lesquels on actionne ce dispositif : une pièce en rupture de stock, des défauts créés ou détectés, des dysfonctionnements sur les outils ou machines ou encore l’apparition d’un problème de sécurité.
Les Flux Continus
L’un des éléments du système Juste à Temps, c’est le flux continu par lequel la production en cours avance sans à-coups d’une phase de fabrication à l’autre avec un minimum (ou pas) de stocks intermédiaires entre chaque étape.
Le Flux se traduit par : comment les pièces se meuvent tout au long du processus, entre chaque poste de travail et ce que cela donne de minute en minute, d’heure en heure, d’une équipe à l’autre, d’un jour, semaine ou mois à l’autre.
Avec une cartographie de la chaîne de valeur on peut visualiser le flux de production en définissant quelles composantes du processus peuvent circuler aisément, quelles composantes requièrent une réorientation et quelles sections nécessitent le plus haut niveau de contrôle.
Le Kaizen / L’Amélioration continue
S’appliquant à n’importe quel type d’organisation, le Kaizen décrit une amélioration continue qui implique tout le monde. Le terme fait habituellement référence à de petites étapes de perfectionnement constant sur une période de temps soutenue.
Le Kaizen se déroule en général sur le lieu de travail appelé “Gemba”. C’est cette amélioration continue de votre chaîne de valeur entière, que ce soit au niveau d’un ou de l’ensemble des processus, qui constituera la globalité de votre activité. Le Kaizen, c’est fondamentalement une manière de penser, une mentalité en vue d’améliorer votre business, votre personnel et vos processus.
Les tableaux de bord Kamishibai (Tableaux de Tàches Rouge et Vert)
Un système qui utilise des cartes en forme de T pour baliser les tâches routinières sur le lieu de travail. Dans un cas d’application classique, les balises sont rouges d’un côté et vertes de l’autre. Au départ on aperçoit la face rouge, puis on les retourne pour afficher la face verte une fois la tâche effectuée.
On peut utiliser les tableaux de bord Kamishibai tant au niveau de l’usine que dans les bureaux pour y suivre les tâches administratives.
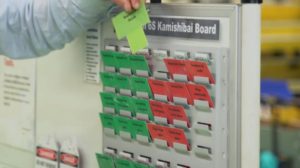
Les systèmes Kanban
Un processus qui vise à signaler un besoin : dans le cas de la Production, la nécessité de fabriquer un produit ou de s’en approvisionner. Le signalement est, pour le Kanban, un indicateur physique: cela peut être une carte, un carton vide ou un chariot en retour. Mettre en place le système Kanban, cela consiste à souligner tous les besoins de votre système de production. Contrôler régulièrement le système pour vérifier que tous les Kanbans sont présents et le sont là où il le faut.
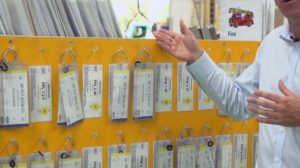
Le TRS
Le TRS est un outil de mesure des performances communément utilisé pour surveiller les améliorations réelles d’un processus, domaine ou machine. Le TRS a été conçu pour indiquer l’efficacité d’une opération industrielle.
Le TRS peut s’avérer un critère de mesure compliqué à comprendre étant donné qu’il provient de trois éléments de calcul: Disponibilité, Performance et Qualité- (DPQ)
- D= Représente le pourcentage de temps prévu pendant lequel l’opération est disponible. Fréquemment appelé “Uptime”.
- P= La cadence réelle de fonctionnement d’une machine calculée en pourcentage de la cadence prévue lors de sa conception.
- Q= Les Bonnes Unités produites en pourcentage par rapport au Total Cumulé d’Unités.
TRS = (DxPxQ)
Le PDCA (Planifier / Faire (Do) / Vérifier / Ajuster)
Le PDCA est une méthode interactive de management en quatre étapes utilisées pour le contrôle et l’amélioration continue des processus et des produits. C’est essentiellement une méthodologie de résolution de problèmes.
PLANIFIER :
C’est la phase dans laquelle vous examinez la situation et déterminez les étapes requises pour la solution du problème. Vous devrez définir des critères de mesure SMART (simples, mesurables, atteignables, réalisables et traçables) si vous voulez que votre plan soit couronné de succès.
FAIRE :
Au cours de cette phase, vous allez appliquer la solution précédemment planifiée. Il peut y avoir un mini cycle PDVA à chaque phase d’implémentation : planifier ce qu’on va faire, le faire, vérifier cette partie et l’ajuster avant de passer à la prochaine grande étape.
VÉRIFIER :
Le simple fait d’avoir mis en place une solution ou un nouveau système ne veut pas dire que vous avez terminé. Il vous faudra vérifier si son implémentation est efficace. C’est ici que nos indicateurs SMART vont vous aider. Si l’on ne peut pas mesurer les résultats, comment saurons-nous si nous avons agi comme il le fallait ?
AJUSTER :
Il s’agit maintenant de recouper les conclusions avec notre plan. Si nous avons atteint les résultats escomptés, nous allons consigner et standardiser le processus. Si la solution adoptée ne donne pas satisfaction ou pas complétement, il faudra comprendre ce qui n’a pas fonctionné, modifier la solution ou le cas échéant créer un nouveau plan, le mettre en application et vérifier comment cela a marché cette fois-ci.
Le Poka-Yoke (Méthodes anti-erreurs)
Une méthode qui prévient ou détecte les défauts que présentent les produits. Le Poka-Yoke consiste à utiliser tout dispositif ou méthode qui fera que l’erreur sera impossible à commettre ou la rendra détectable immédiatement. C’est un outil d’analyse de processus classique.
La Maintenance Productive Totale
La Maintenance Productive Totale est l’un des outils d’entreprise Lean les plus avancés. Une fois que le flux de Production, l’entretien des postes de travail et les bonnes pratiques sont en marche, il devient important de maintenir le temps de disponibilité de votre machine à un niveau optimal.
Fonctionnant parallèlement, c’est à dire en suivant de près et fidèlement le 5S, la MPT est le processus par lequel l’opérateur s’engage à faire la maintenance régulière et quotidienne de sa machine. Cette dernière doit être méticuleusement nettoyée, tout problème d’entretien doit être résolu. L’objectif est de remettre l’engin à l’état neuf.
La Cartographie des Chaînes de Valeur
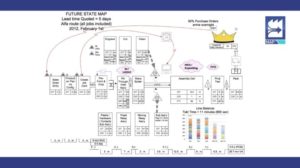
Une Cartographie de la Chaîne de Valeur aide à appréhender le niveau de gaspillage dans votre processus et à l’éliminer. A cartographie de la chaîne de valeur est une puissante technique Lean qui est utilisée pour documenter, analyser et améliorer les flux d’information et des matériels requis pour un processus. La cartographie de la chaîne de valeur actuelle identifie la valeur et le gaspillage dans un processus de flux permettant le développement d’une “cartographie future” afin d’éradiquer le gaspillage. Toyota a créé cet outil en l’appelant “Charte de Flux d’Information et de Matériel”.
Assurez-vous d’avoir une stratégie et des outils en place: Contactez dès aujourd’hui notre expert TXM