Les 3 étapes pour standardiser le travail
La standardisation du travail est l’un des piliers sur lesquels repose la démarche Lean dans sa quête de l’Excellence Opérationnelle. Il y a trois étapes fondamentales pour la création du travail standard : La définition du résultat à atteindre, la standardisation de la méthode et la standardisation de l’amélioration de la méthode. Ces trois étapes sont utilisées pour créer des processus robustes, simples et efficaces que n’importe qui dans l’entreprise peut utiliser.
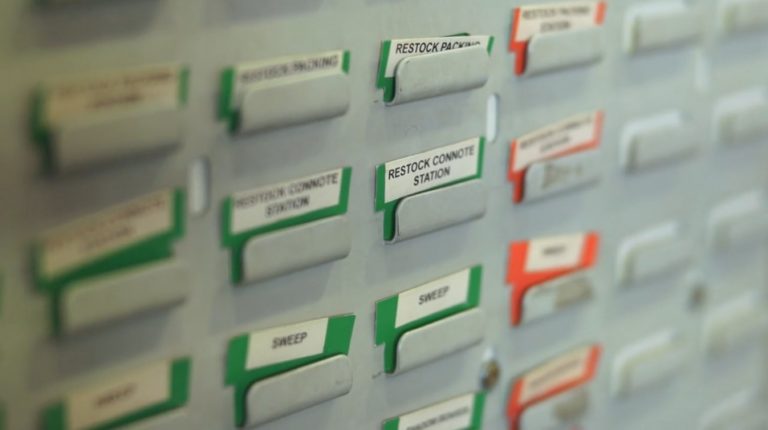
-
Définir le résultat à atteindre
Avant même de se pencher sur la manière dont le travail doit être fait, il est impératif de s’entendre sans équivoque sur ce qui doit être fait. Sans une définition rigoureuse du résultat qu’il faut obtenir, les discussions tournent autour de « la meilleure méthode » alors que les conceptions de ce qui est exactement attendu comme produit de cette « meilleure méthode » sont souvent différentes ou incohérentes.
Cela peut sembler très élémentaire, mais il est fondamental pour toutes les parties prenantes de disposer d’un référentiel commun. Le propriétaire du processus (celui qui exécute la méthode) agit en tant que « fournisseur » (interne) pour satisfaire une demande « client » (interne aussi) parfaitement exprimée. Dans un environnement de production, cela peut être extrêmement technique pour ce qui est des spécificités produit. Dans un environnement de service, cela nécessite que les experts concernés s’entendent sur ce que le processus doit exactement fournir.
Dans tous les cas, il faut penser à impliquer toutes les parties prenantes pour définir le résultat de la méthode, avant de définir la méthode elle-même. Ce résultat doit pouvoir être caractérisé en termes quantitatifs et qualitatifs.
Il en va de même lorsqu’on accueille de nouveaux collaborateurs : Ils doivent comprendre tout d’abord quelle est le résultat à atteindre, à quel client interne il est destiné et pourquoi, avant de leur apprendre la méthode en elle-même.
-
Standardiser la méthode pour atteindre le résultat
Dans leur célèbre article, Spear & Bowen affirment que l’un des éléments clés de l’ADN du système de production Toyota est que tout le process est hautement standardisé en termes de méthode, de timing et de séquence. Au fil du temps, Toyota décortiqua chaque process en sous-tâches et petites étapes pour définir parfaitement le timing et la séquence de la méthode et créer ainsi un travail standardisé.
Trop souvent nous observons l’un des propriétaires du processus (cela peut être un opérateur dans une usine, un gestionnaire d’appro dans un service achats ou un ADV dans un équipe commerciale) appliquer une méthode différente de celle de son collègue. Lorsque nous l’interrogeons à ce sujet, invariablement les réponses sont « J’ai ma propre méthode » ou « ça revient au même ».
La réussite de la standardisation du travail implique nécessairement la compréhension de son intérêt. Dans le Lean, le travail standardisé n’appartient pas à l’individu, mais au processus. Cela ne revient jamais au même car deux méthodes différentes ne fourniront pas le même résultat que si par hasard les avantages de l’une sont compensés par les désavantages de l’autre. Aucune des deux ne sera pas optimisée et toutes les deux seront tributaires du bon vouloir de celui qui l’exécute.
Un bon point de départ pour standardiser une méthode c’est de réunir un groupe de personnes de différents niveaux d’expérience et faire en sorte que chacune dresse sa liste de tâches. Ensuite, le même groupe analyse les étapes et se met d’accord sur leur définition. La sécurité étant un facteur clé, une évaluation de risques peut réduire les contraintes ergonomiques et aider à définir la meilleure séquence de mouvements.
Une fois cette étape franchie, le groupe pratique la séquence jusqu’à ce que chacun puisse faire le travail de mémoire, sans hésitation. Pour un cycle court de moins d’une minute, cela peut représenter environ 30 fois. Pour des cycles plus longs, chaque personne réalisera probablement la tâche une seule fois et une personne sera chargée d’en faire la synthèse.
La méthode qui en résulte est la somme des temps les plus courts pour chaque étape et constitue donc « la meilleure manière connue d’atteindre le résultat ». En appliquant cette méthode et que cette méthode, le résultat est atteint à chaque fois, toutes les fois. Cette méthode devient le standard de travail. Le standard doit être matérialisé (fiche au poste, procédure de travail, gamme de montage, gamme de contrôle, …)
-
Standardiser la manière d’améliorer la méthode
Dans le Lean, nous concevons le travail standard comme « la meilleure manière connue d’atteindre le résultat ». Voilà qui introduit la notion d’amélioration continue inhérente au Lean. Le travail standard n’est pas un cadre rigide et immuable. Au contraire, au fur et à mesure que les propriétaires du processus appliquent la méthode, des pistes d’amélioration apparaissent. Des évolutions technologiques peuvent aussi contribuer à remettre en question la méthode qui fait l’objet du standard.
En revanche, le processus pour faire évoluer la méthode est lui aussi standardisé. La modification proposée est tout d’abord décrite, puis essayée et le résultat vérifié. Les possibles effets indésirables sont évalués en suivant un plan de levée de risques spécifique. Une fois la nouvelle méthode entérinée, un nouvel standard est matérialisé et les équipes sont formées et informées de manière à ce qu’il soit adopté en bloc. En cas d’effet secondaire imprévu, le retour immédiat au standard précèdent permettra d’étudier sereinement les raisons pour lesquelles la nouvelle méthode ne fournit pas le résultat attendu.
Le rôle des superviseurs et responsables d’équipe est décisif pour inciter les propriétaires des processus à identifier les améliorations à apporter, mais aussi pour cadrer toute tentation de s’écarter de la méthode et introduire pêle-mêle des modifications, même si elles s’avèrent efficaces. Encore une fois, l’amélioration continue appartient au processus, pas à l’individu.
La standardisation des processus entraîne un changement progressif de l’efficacité globale. C’est un effort collectif où toutes les parties prenantes sont mises à contribution. Sans travail standard, les bonnes idées ne sont pas capitalisées par l’entreprise, et il arrive un moment où elle n’avance plus.