Comment utiliser le Lean dans la configuration d’une usine
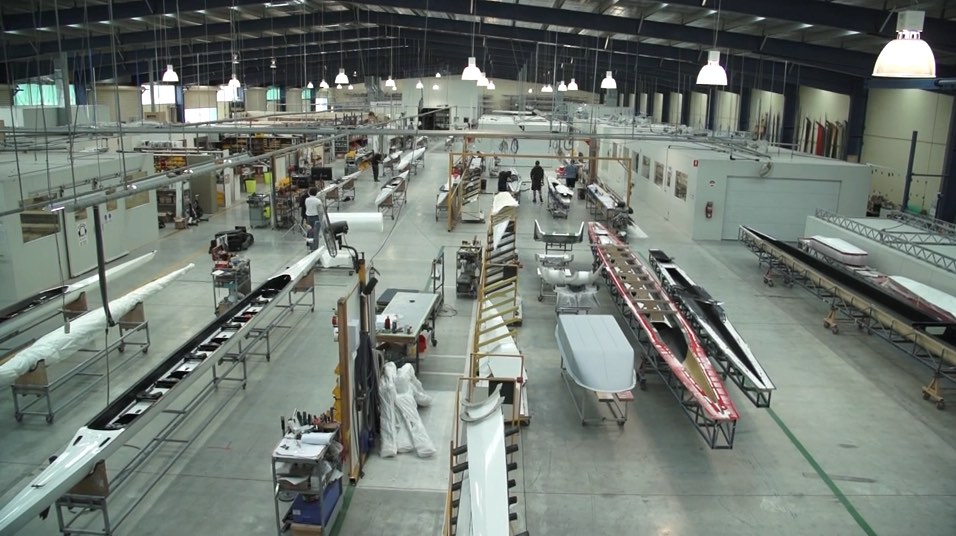
L’une des clés de réussite de la gestion d’une usine est de disposer d’une configuration efficace. Elle aura un effet direct sur l’ensemble du fonctionnement de votre entreprise, y compris les processus de production, les stocks, l’expédition et l’administration.
Chez TXM, nous considérons qu’une configuration d’usine est efficace lorsqu’elle applique les principes du Lean. Comme vous le savez peut-être déjà, le Lean élimine les gaspillages et apporte de la valeur à vos clients en réduisant les coûts, en améliorant la qualité, en réduisant les délais de livraison, en améliorant la sécurité et en renforçant la motivation des équipes.
Il existe plusieurs facteurs qui différencient une configuration d’usine en mode Lean d’une configuration traditionnelle.
Se baser sur les Processus versus se Focaliser sur la Chaîne de Valeur
Une configuration traditionnelle d’usine se focalise davantage sur des ateliers basés sur les processus : Typiquement, les machines de même type sont regroupées ensemble. Une usine traditionnelle de fabrication est divisée en ateliers de découpe, de fabrication, d’usinage et d’assemblage.
La configuration d’une usine en mode Lean se focalise sur la chaîne de valeur, c’est-à-dire toutes les étapes de la fabrication d’un produit allant depuis la commande des matières premières jusqu’à la livraison des produits finis au client.
Les configurations en mode Lean combinent les étapes de production avec une orientation produit à travers l’usine, comparée aux regroupements de processus présents dans une configuration traditionnelle. Dans une configuration en mode Lean les processus sont reliés entre eux dans le sens du produit fini. Les besoins en manutention et manipulation qui en résultent sont beaucoup moins importants.
Coût unitaire versus Flexibilité
Au lieu d’utiliser des machines très grandes, impossibles de déplacer facilement dans des configurations d’usines traditionnelles, les configurations en mode Lean privilégient des équipements plus petits et dédiés à chaque famille de produits. Ainsi, des équipements de taille appropriée sont sélectionnés pour répondre à la demande de la chaîne de valeur, c’est-à-dire aux changements rapides pour des lots de plus petites tailles.
Design versus Contrôles visuels
Les usines sont censées être fonctionnelles. Parfois, certaines considérations esthétiques peuvent l’emporter sur le bon sens. Les configurations d’usines en mode Lean disposent généralement de peu de place entre les machines, ce qui empêche l’accumulation d’en-cours intermédiaires et réduit les mouvements inutiles des hommes et matériaux.
En générant moins de gaspillages, les excès de produits seront réduits, tout comme la surproduction, les mouvements et les transports inutiles. De plus, lorsqu’il y a du gaspillage celui-ci devient visible. La configuration des installations en mode Lean permet de rationaliser les flux de personnes, de matériel, de produits et d’informations, et d’utiliser des contrôles visuels pour rendre visibles les obstacles et les interruptions des flux. Les usines configurées en mode Lean utilisent des contrôles visuels pour une meilleure communication.
Connexion avec la demande Client
Les usines en mode Lean permettent de livrer aux clients des produits sans défauts et dans les délais requis. L’un des facteurs clés d’une installation en mode Lean est que les flux de valeur sont reliés à la commande du client et permettent de répondre rapidement à sa demande.
La configuration d’une usine en mode Lean permet non seulement de relier l’ensemble de la chaîne de valeur aux clients externes, mais aussi de relier les processus aux clients internes.
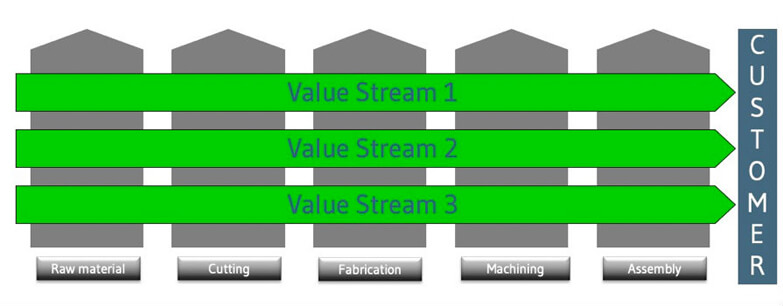
Flux
L’élément essentiel d’une configuration d’usine en mode Lean est le flux. Dans un autre article de TXM, nous avons évoqué les “7 flux à prendre en compte lors du design de la configuration de votre usine”.
Il s’agit des flux de matières premières, d’en-cours, de produits finis, de consommables, de mouvements de personnes, de déchets et d’informations. Les longues distances, les longs délais d’installation, les grosses machines pour les productions de gros lots, une mauvaise maintenance et les goulots d’étranglement des processus constituent des obstacles classiques aux flux.
Une bonne implantation permettra à ces flux de circuler efficacement dans tous les processus. Nous utilisons le terme “flux de valeur ou chaîne de valeur” pour décrire les activités à valeur ajoutée qui y sont rattachées.
Moins de gaspillage
Une mauvaise implantation embarque fatalement des inefficacités qui seront ressenties au quotidien. Les configurations en mode Lean génèrent moins de gaspillages et favorisent l’amélioration continue. Le flux continu permet une production constante, avec moins de stocks et de temps d’attente.
Les espaces plus petits entre les machines réduisent non seulement les mouvements des opérateurs, mais rendent également difficile la surproduction. La place pour les en-cours de production est dimensionnée avec le même niveau d’exigence que l’implantation des machines elles-mêmes, donc vous êtes obligé de corriger les causes qui génèrent les en-cours excessifs.
Moins de gaspillage
Une mauvaise implantation embarque fatalement des inefficacités qui seront ressenties au quotidien. Les configurations en mode Lean génèrent moins de gaspillages et favorisent l’amélioration continue. Le flux continu permet une production constante, avec moins de stocks et de temps d’attente. Les espaces plus petits entre les machines réduisent non seulement les mouvements des opérateurs, mais rendent également difficile la surproduction.
La place pour les en-cours de production est dimensionnée avec le même niveau d’exigence que l’implantation des machines elles-mêmes, donc vous êtes obligé de corriger les causes qui génèrent les en-cours excessifs.
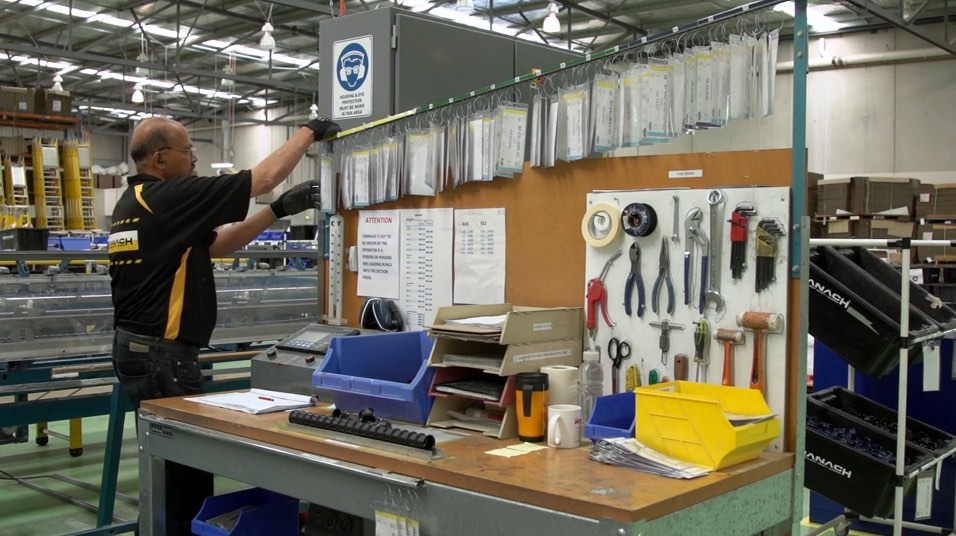
Flexibilité
Une nouvelle implantation vous permettra d’envisager une série de changements : une plus rapide expansion due à l’augmentation de la demande, au lancement de nouveaux produits, aux changements de méthodes ou d’équipements, ou pour répondre aux exigences en matière de sécurité et d’environnement. Il est donc essentiel de concevoir une configuration qui soit suffisamment flexible pour s’adapter aux changements futurs.
Un nouveau standard
Une configuration en mode Lean ne doit pas être élaborée par une seule partie prenante. Au contraire, cela doit être le fruit d’un effort de collaboration de la part d’un ensemble de parties prenantes de l’entreprise.
L’intégration des différents points de vue dans la conception de la configuration de l’usine et leur contribution au développement des plans d’aménagement est essentielle pour que la transformation de l’usine soit un succès.
N’oubliez pas que la conception parfaite d’une usine, n’existe pas ; vous aurez toujours une marge de manœuvre pour poursuivre l’amélioration continue.