Client Haymes Paint
Le défi
Notre client est un fabricant de peinture de taille moyenne. Il avait beaucoup investi dans un système ERP et utilisait la fonctionnalité MRP de ce système pour planifier sa production. L’utilisation du MRP implique d’abord l’introduction d’une base de données dans votre système pour chaque client, produit, pièces et matières utilisées, et opérations.
En plus, un ensemble de paramètres du programme directeur de production (PDP) est établi, et il génère des données sur la taille optimale des lots, les délais et les besoins en stock de sécurité.
Notre client utilisait ces informations pour élaborer une prévision hebdomadaire et saisissait les informations dans le système ERP. La fonctionnalité MRP opérait pendant la nuit et a programmait le temps de production, les matériaux et les stocks nécessaires pour répondre aux exigences de la prévision.
En termes de Lean Manufacturing, nous appelons cela la planification « push », où l’approvisionnement en matières premières et les encours sont poussés à l’étape de production suivante en prévision de la demande future. Le problème, bien sûr, était de prévoir la demande pour chaque produit et chaque semaine. Malgré beaucoup d’efforts, un stock élevé et une précision de prévision relativement bonne, le client avait toujours des problèmes de pénurie et de commandes urgentes dans la production.
La solution TXM
En travaillant avec TXM, le client a cartographié la chaîne de valeur de son processus de production. Nous nous sommes concentrés sur la réduction du délai entre le moment où le besoin d’un lot de production est déclenché et celui où le lot finalisé est remis au stock.
Le délai a été ramené d’environ trois semaines à cinq jours. La taille des lots a également été réduite afin de permettre à l’entreprise d’assurer un cycle de production plus rapide.
Le cas échéant, l’accent a été mis sur la réduction des délais de changement de lot afin que les petits lots puissent être réalisés sans compromettre l’efficacité.
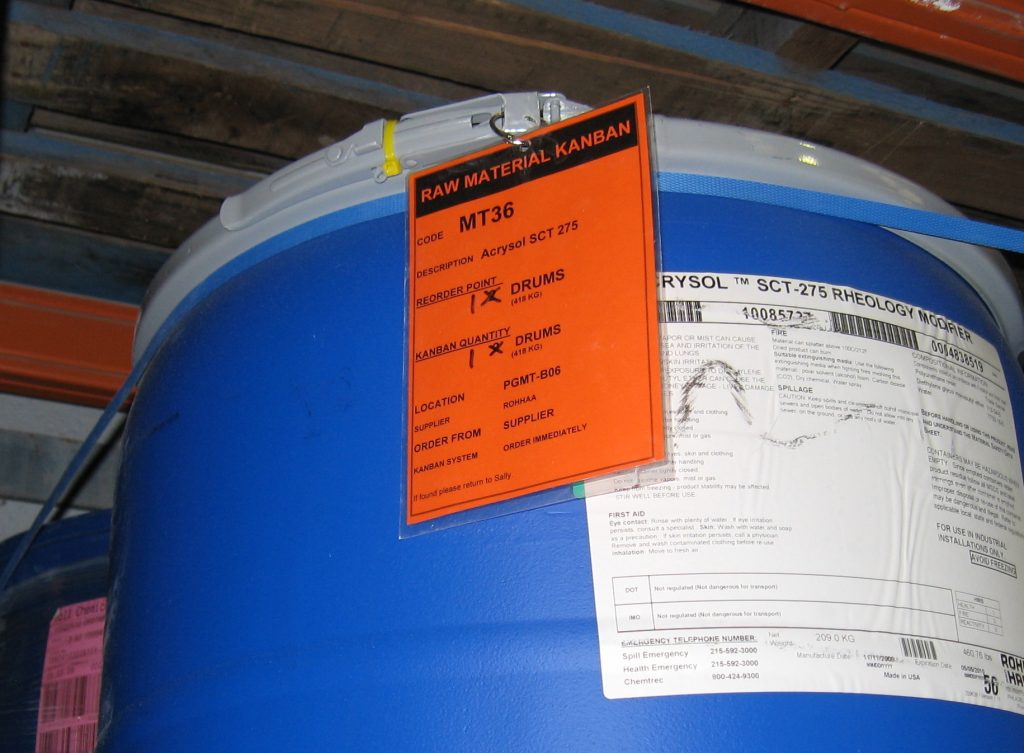
Le résultat
L’élément déclencheur de la production a basculé de la prévision au besoin, en instaurant un système Kanban. Les ventes quotidiennes de produits sont devenues l’élément déclencheur du remplacement des stocks.
Un rapport était envoyé chaque jour par le centre de distribution à l’usine. Ce rapport indiquait au planificateur de la production les produits qu’il devait fabriquer ensuite.
Le niveau du stock de produits finis était déterminé à partir du délai nécessaire pour réapprovisionner le lot et de la taille du lot. En conséquence, le stock de produits finis a été réduit de 30 %, et les ruptures de stock ont été réduites à presque zéro.