Mise en œuvre d’une configuration d’usine en mode Lean : Leçons pour directeurs d’usine et directeurs des opérations
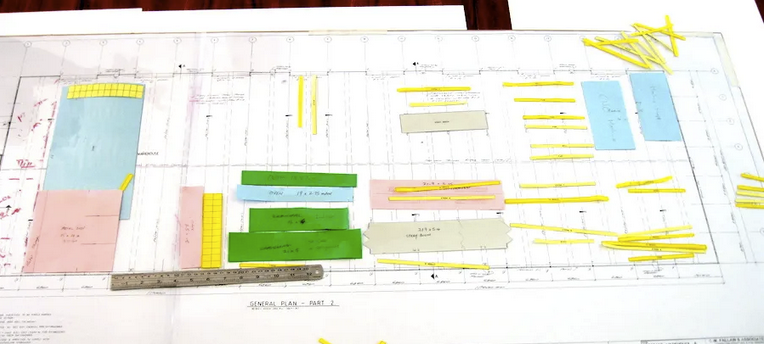
En tant que directeur d’usine ou directeur des opérations, l’un des projets les plus passionnants que vous puissiez avoir est de mettre en place une nouvelle usine. Au cours de ce processus, le développement d’une configuration en mode Lean est l’une des étapes les plus délicates.
Chaque directeur d’usine ou des opérations a sa propre vision de l’implantation idéale de son usine. Cependant, évitez de vous lancer seul dans ce projet – obtenir un soutien externe et impliquer toutes les parties prenantes vous permettra d’obtenir un bien meilleur résultat.
J’ai réalisé ma première configuration d’usine en 1990, alors que j’étais un tout jeune directeur d’usine. Avec l’ingénieur de projet, nous avons déterminé l’emplacement des nouvelles machines, puis nous l’avons dessiné. J’ai regretté cette approche. Chaque fois que je me promenais dans l’usine, un opérateur me faisait remarquer que les panneaux de commande étaient mal placés ou qu’il n’y avait pas assez de place pour les matières premières dans la zone de pesage.
Les ingénieurs de maintenance me rappelaient combien il était difficile d’accéder aux armoires électriques pour la maintenance de routine et l’équipe de sécurité nous a obligé à effectuer des changements coûteux pour réduire les risques que les chariots élévateurs pouvaient causer.
La leçon à tirer de cette expérience est d’impliquer toutes les parties prenantes. Chez TXM, nous recommandons une équipe de 6-10 personnes au plus, composée d’experts et de décideurs. Vous avez besoin des deux, car parfois les experts ne peuvent pas prendre de décisions seuls et souvent les décideurs n’ont pas une connaissance détaillée du processus. Les principales parties prenantes à consulter sont les suivantes :
- Ventes et marketing : nous avons travaillé avec une entreprise dont les avis des employés divergeaient sur la quantité idéale d’armoires à produire par jour. Certains pensaient que 80 armoires par jour seraient suffisantes, tandis que d’autres voulaient que la capacité soit de 120 armoires par jour.
Les répercussions de cette disparité dans les volumes à produire pouvaient être considérables, puisque le bâtiment que l’entreprise souhaitait exploiter ne pouvait pas répondre à la demande de 120 armoires par jour. De même, nous avons connu des cas où des ingénieurs et des responsables de production ont installé de gros équipements de production hautement automatisés et peu flexibles à un moment où la demande était tournée vers des produits plus diversifiés et des séries de production plus courtes. Vous devez donc commencer par obtenir une vision claire et partagée de ce que l’usine est censée produire. - Opérateurs d’usine : en général, nous impliquons un ou plusieurs chefs d’équipes dans la conception de la configuration de l’usine. Ces personnes travaillent directement sur les lignes de production et ont des idées précises et des avis pertinents sur la façon de bien organiser et disposer les choses.
Par exemple, le meilleur emplacement pour les panneaux de contrôle ou pour les matières premières ou consommables les plus utilisés.
- Ingénieurs de maintenance : dans la disposition des équipements, l’accès pour les opérations de maintenance est une considération essentielle. Si un équipement essentiel est très difficilement accessible pour sa maintenance, cela peut entraîner des temps d’arrêt et des coûts considérables.
- Équipe chargée de la logistique : dans la plupart des usines, les matériels et produits ainsi que les voies pour les acheminer peuvent prendre plus de place que les lignes de production. Il est donc important que le stockage et la circulation des matières premières, des en-cours et des produits finis soient soigneusement pris en compte dans chaque configuration.
- Planificateur de production : le responsable de la planification de la production est souvent le mieux placé pour savoir comment l’usine doit tourner pour répondre à la demande des clients. Cela peut avoir une incidence considérable sur la taille des lots et les niveaux de stock tout au long du process.
- Ingénieurs de projet : ceux qui construiront la nouvelle installation doivent bien entendu participer à l’élaboration de la configuration de l’usine. Ils doivent comprendre la finalité de la configuration afin de ne pas apporter lors de sa mise en place de modifications qui pourraient compromettre son efficacité. De plus, ils pourront se faire une idée précise des différents facteurs contribuant aux coûts du projet. Par exemple, l’installation d’un équipement gourmand en énergie loin de l’alimentation électrique principale peut entraîner des coûts de câblage considérables. Il est souvent possible de remédier facilement à ce genre de problème en inversant la configuration pour rapprocher les machines clés du tableau de distribution (sans compromettre ni la logique ni la finalité de la nouvelle configuration).
- Responsable HSE : la plupart de pays exigent que toute nouvelle installation ou tout nouvel équipement fasse l’objet d’une analyse de risques. L’implication de votre responsable HSE dans l’équipe de conception évitera que des éléments à risque apparaissent.
Il y a probablement d’autres personnes qui devraient être impliquées dans le processus. Cependant, il y a un membre de l’équipe que nous recommandons vivement : un facilitateur externe. En associant à votre équipe un expert en configuration d’usines en mode Lean ayant des connaissances pratiques en matière de production, vous pourrez être certain que chaque personne pourra s’exprimer et être écoutée.
Chez TXM, notre processus de configuration d’usines est une démarche très structurée et efficace que nous avons appliquée dans plus de 200 projets à travers le monde. Ainsi, nos consultants peuvent avoir accès à une énorme base d’alternatives de configuration. En général, pour une surface d’usine donnée nous obtenons un rendement supérieur d’environ 30 % ; une productivité supérieure de plus de 20 % ; et des réductions de délais de plus de 50 % par rapport aux approches traditionnelles en matière de conception de configurations.
Les principaux enseignements que les directeurs d’usine et les directeurs des opérations peuvent tirer de la conception d’une configuration d’usine en mode Lean sont : ne vous lancez pas seul, faites participer toutes les parties prenantes et demandez l’aide d’un expert.