Client SCD Remanufactured Vehicles
Location Brisbane, Australia
Driving Cultural Change Through the Optimal Transfer of Information & Materials
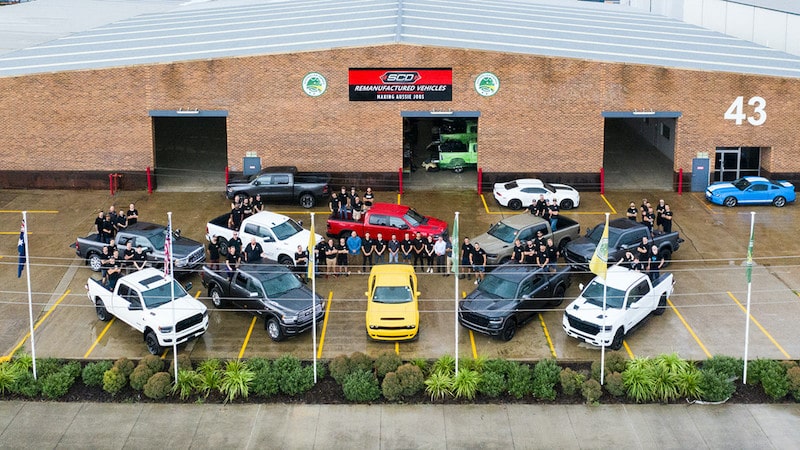
Background
SCD Remanufactured Vehicles is a company based in Queensland, Australia specialising in importing and selling American-made trucks, SUVs, and cars. The company has been in business for over 20 years and built a reputation for providing high-quality vehicles to customers across Australia.
One of the main focuses of SCD Remanufactured Vehicles is the conversion of American-made vehicles to comply with Australian Road Standards. They do this with their innovative Steering Transfer® Technology. The technology is the world’s first ADR-approved steering transfer system with zero-play/backlash. They also provide their customers with a wide range of American-made vehicles that are not readily available in the Australian market. SCD imports a variety of popular American brands such as Chevrolet, Ford, Dodge, and Nissan.
The Challenge
SCD contacted TXM in Brisbane, Queensland to help them analyse and improve their operational capacity, performance, and culture within the manufacturing facility. SCD employ around 50 staff at a large site which is suited to the scope of work and desired future capacity. The site has several vehicle conversion bays, a dash conversion bay, as well as heater box manufacturing and a fabrication cell.
The facility lacked visual management, visual controls, and performance metrics. SCD had been using a workshop management application to track the status of vehicles, but the application was not actively used and the only way to know the status of a vehicle is by asking the technician.
At times senior management had found themselves on the factory floor assessing technical and quality issues. These issues took senior management away from growing the business in a meaningful way. Fixing these issues would help SCD’s potential within the market and allow the senior managers to focus on business innovation and growth.
SCD had built a strong foundation to improve on. For SCD to realise its potential, it needed to create mature and robust business processes, management systems and an operational structure built to support the whole organisation. SCD were producing a steady number of vehicles but were looking to increase production capacity due to increasing organic & forecasted demand for American-made vehicles in Australia.
The Solutions
TXM created a year-long three-phase plan to analyse, assess, implement, and sustain changes to their operations to achieve the robust targets set out by SCD. TXM supported SCD with every element and helped them sustain the results by implementing strong business process systems via the TXM Manufacturing Agility Process® (MAP).
Phase 1 – Discovery
The first phase of the operational improvement project was the discovery phase where the whole current state value stream was mapped using the TXM Manufacturing Agility Process (MAP®). Several key people in the business met with the TXM consultant on-site for the current state mapping session to map every process from the first information flow to raw material forecasting through to certification paperwork, as well as material flows from receipt of raw materials to vehicle despatch.
The sessions identified areas across the business where changes could be made to increase productivity, improve information flow, and increase customer service. Firstly, the current state revealed excessive waste across production processes including excessive work in progress (WIP) and no clear structure around production scheduling.
Secondly, the MAP® analysis uncovered a disconnect between the engineering and production teams creating silos within the business with contradicting KPI’s. Finally, the current state highlighted a lack of quality procedures and there was no regular communication of daily challenges and issues.
Phase 2 – Implementation
The second phase of the operational improvement project saw the findings from the current state map implemented to realise the future state map or the most optimal configuration for the business from order to delivery. The future state saw the detailed process mapping of all workstations with reduced WIP through the reduction of workstations within workstations.
Next, takt-times (the rate at which products must be produced to meet customer demand) were defined allowing all workstations to be balanced according to the optimal production flow. Lastly, a “Pulse System” was established to help achieve the daily output targets.
Phase 3 – Sustaining and Improving
The final phase at SCD Remanufactured Vehicles was to sustain the improvements and changes implemented in the second phase. This saw a cultural change within the organisation with staff becoming advocates for change. 5S was implemented across the business creating a clean and organised work environment improving efficiency and safety. Visual performance boards and KPI’s in each department provide a clear visual representation of performance metrics, making it easier to track progress and identify areas for improvement.
Leader Standard Work and daily stand-up meetings were implemented to measure performance against the KPI’s and the ability to identify roadblocks hindering progress became easier for senior managers and drove a cultral change. The teams were taught the fundamentals of Root-Cause Analysis and Problem Solving to improve performance by identifying the underlying causes of the problems and implement effective solutions.
The final major change to aid the continued success of the operational improvement project was the delivery of parts to assembly areas as kits to ensure all necessary components were available when needed minimising delays and improving overall productivity.
The Results
“The support from the TXM team was invaluable. TXM helped create a systematic approach to process improvement the whole team were able to get behind. Everyone now understands their roles and are more motivated, we have seen a huge cultural change. The teams now communicate more with less frustrations. Not to mention the production cells and factory floor are more organised and much safer.” James Brycker – Chief Manufacturing Officer – SCD Remanufactured Vehicles
The team at SCD with the help of TXM were able to achieve major improvements across the business over the year-long project including better information flow, greater visibility of WIP and problems, and robust business processes. The TXM Support at SCD Remanufactured Vehicles resulted in:
- Daily output of the factory increased by 35%
- Work in progress reduced by 60% or the equivalent to over $1M reduction of assets on shopfloor
- Lead Times reduced by 74%
- Floor space required in Sub-Assembly areas reduced by up to 50%
- Direct Labour costs reduced by 55%