Where to Start?
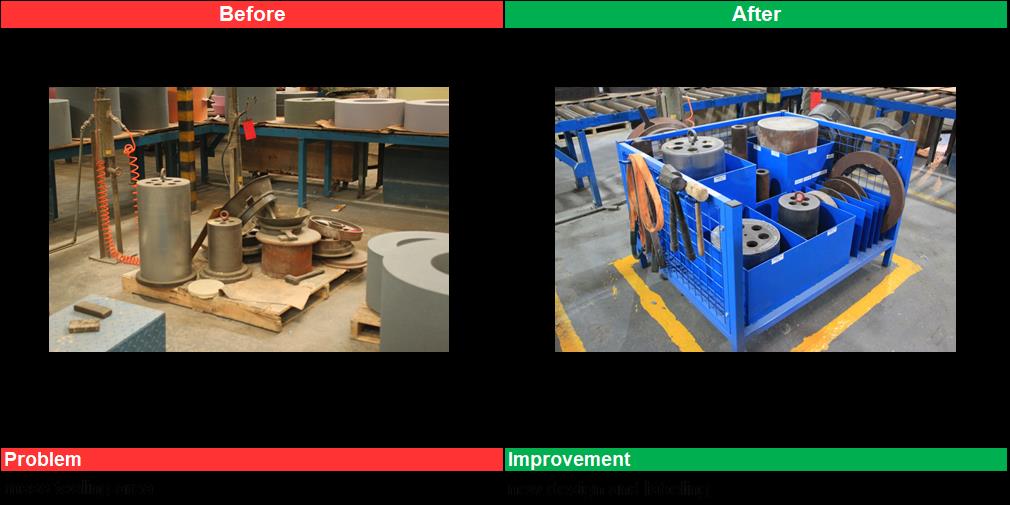
To have an organised and efficiently running factory, we need to know that everything has a place, is in that place and is clean and ready for use – this is the basic premise for the Lean manufacturing tools we use to implement good workplace organisation; 5S. 5S is a systematic approach to workplace organisation. While there are many interpretations of the original Toyota definitions (there is even more than one Japanese version) the principles behind the stages are still the same. Here we will look at the first three “S”’s – the “doing” part of the process. Then we will focus on “sustaining” our workplace organisation efforts.
The 5 S’s
Whether you are beginning 5S or revitalising, chose an area and set aside some time (3 hours at least) to go through the first three stages:
- Sort – go through everything; throw away rubbish, archive old stuff you may need, decide what you need in that area on a daily and weekly basis. Everything else must be removed. Sentiment can not play a part here – this is a manufacturing environment.
- Set in Order – take the items you need in that area on a daily or weekly basis and find the best homes for them; label, mark locations, colour code – make it clear to anyone entering the area what should be where.
- Shine & Clean – as you are setting a location for each item, give it a wipe and check it is in good working order. Any broken item needs to be fixed. If your working area is particularly dirty, more time needs to be set aside so a thorough clean can be completed.
These first three steps will get you well on your way to visually improving your factory. And when our factories look better, our people feel better about working in them – suddenly there is more space to move and those little annoying things are easier to find. The challenge is to continue to maintain this new level of organisation.
This is where the “Standardisation” and “Sustaining” come into play within an organised and efficiently running factory, we need to know that everything has a place, is in that place and is clean and ready for use – this is the basic premise for the Lean manufacturing tools we use to implement good workplace organisation; 5S.
5S is a systematic approach to workplace organisation. Now we have looked at the first three S’s – the “doing” part of the process. Now we will focus on maintaining our good workplace organisation efforts.
The first part of 5S is the easy part, once you get going – we understand how to sort and tidy, as we do it all this time – at home, in our cars, in our garages, for our tax returns (although some people are better at it than others), The challenge is to maintain the new level of cleanliness and improve on it as time progresses; not to let it naturally let is slip back. This is where the last two “S”’s come into the process.
- Standardisation – the new arrangement and level of cleanliness is our new standard for each area. Take photos and display in the area; talk about the 5S activities in your toolbox talks and daily meetings; share ideas across the factory. This helps to create your new 5S standards and brings consistency across the factory.
- Sustain – if the first 4 S’s have been done well, sustaining the cleanliness and origination becomes simpler as it is clear where everything goes and each person working in an area knows where to return things at the and of the job or end f the shift. Using simple audits, we can track how we are going to maintaining our 5S baseline on a weekly basis and to also note the areas of improvement we need to make in the week ahead.
Where ever you are in your Lean Manufacturing implementation, using 5S as your workplace organisation tool ensures you are keeping on track and involving every person in your factory. If you are a little lost or have fallen behind, then start the process again; get back to Sorting and Setting in order. This is the foundation of your Lean production system and you can make it work.