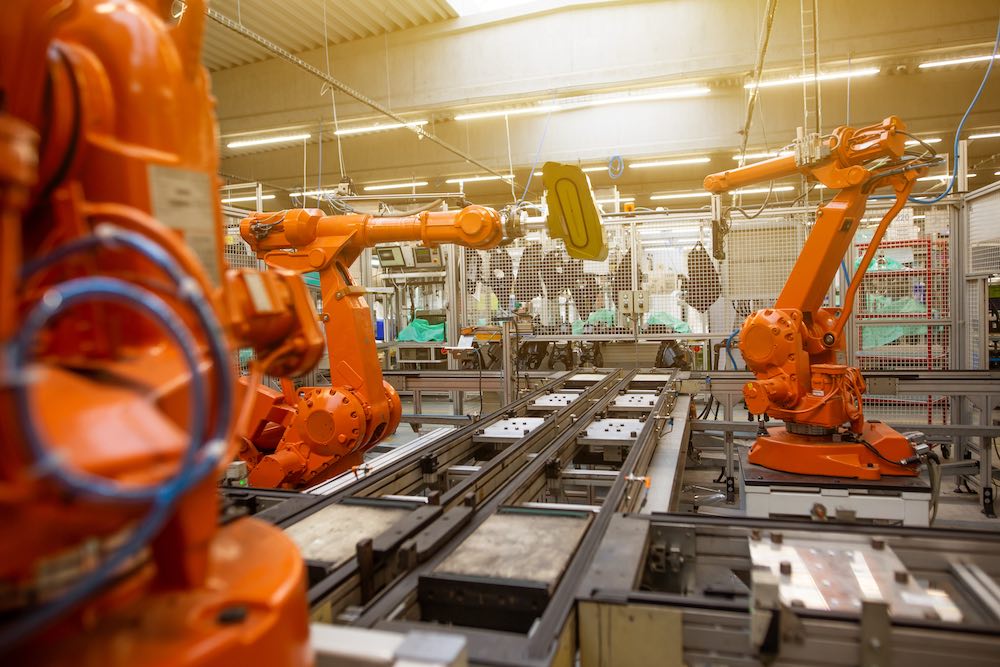
Leveraging Digital Solutions in a Lean Management System
The Industry 4.0 revolution has spawned a bewildering array of software solutions aimed at delivering operational data to operational leaders. A recent trade exhibition I attended featured an entire section on Manufacturing Execution Systems, with at least a dozen different software tools offering to improve operational performance.
Never have businesses had access to so much data on the state of their process. This provides a tremendous opportunity for effective short interval control. That is, tracking performance at as short an interval as possible and taking preventative or corrective action as issues occur in as close as possible to real time.
However, the challenge is what to do with all this data. I like to say that software does not solve problems – people do. Brilliant analysis and easy to read dashboards are only effective if leaders take action to correct problems or poor performance when it is highlighted. Removing the human element from data collection can lead to a loss of employee engagement. When the team leader in a work area has to collect the data on his team’s performance and record it on a handwritten graph on a visual management board, they have ownership of that information and view it as theirs. In many cases they systems are -one-way, presenting data, but providing no mechanism for feedback or problem solving.
If the data is simply presented to them on a screen, after a few weeks, they may not even notice the actual performance. It is not uncommon for me to walk through a factory with live electronic dashboards showing off target performance through the factory and this is simply being ignored. Even worse, many systems require front line staff to enter large amounts of data to provide reports to their managers, who they rarely see. In this case software can even be seen as an extra chore and resented by the very people it should help.
So how do you avoid these problems make the most of these amazing digital tools that are now available?
Remember Where the Value is Created
As a manager, it is great to have tools that provide you with a live and accurate view of operational performance, enabling you to slice and dice data and produce impressive reports for senior leadership. However, this can perpetuate a top-down model where solving problems and making improvement is solely the job of managers and engineers. This approach, which is the norm in many businesses, means that managers and engineers become bottlenecks for improvement and also that response times for issues are usually measured in days or weeks.
The people who create value for your customers are your front-line teams. These team members and their leaders also have the best understanding of your process and are best placed to take immediate action when problems occur, minimising their impact and maximising your chance of eliminating the root cause. Therefore, when selecting and developing software solutions, focus first on how front-line teams will use the data.
How will they access the data? How will it help them and will the data be presented in a way that is useful and accessible to the front-line teams. Remember that not everyone understands graphs, so what might look clever and impressive for an engineer may be incomprehensible to a front-line team member. The same simple bar graphs and red-green colour coding that are used on manual visual boards can work effectively in bar graphs or dashboard dials on digital systems.
You should also think twice before completely abandoning manual visual boards. These can complement the digital solutions. Even where touch screens are used to record data and communicate issues, we have observed that the time taken to wrangle the software tool can be distracting and cause a loss of focus during daily stand up meetings compared to filling out a problem solving concern strip by hand.
TXM Consulting Director, Anthony Clyne, explains this extremely well in his short video “The data is in the computer”. We have noticed that some of our customers that went fully digital and now re-introducing manual visual management for problem solving daily issues.
Using the Data
Another challenge is to get team leaders and even managers to make effective use of the data presented. Leader standard work can play a big part here. Establish simple routines that require team leaders and managers to check the performance at regular intervals, perhaps hourly for a team leader and every three hours for a manager. If performance is off target, they need to record the root cause and corrective action taken.
An Andon system can be very effective here. This enables team members to flag an issue that they find and then requires the team leader to respond with support in a defined period. If the team leader is unable to resolve the issue, then it can be further escalated to manager or support functions (e.g. the quality team or maintenance) who also have to respond within a defined period. If it is a safety or quality issue, production will stop until it is resolved. Some manufacturing execution systems have Andon built in or can be configured to include an Andon system.
Selecting a System
As I mentioned at the start of this blog, there are dozens of different systems available. They vary in terms of capabilities, cost, and usability. Equipment vendors are often offering MES tools that operate with their machines. These clearly operate seamlessly with the vendors’ equipment, but do lock you in to one brand of machine, which few manufacturers are able to do.
There are also big systems that integrate directly with full suite ERP systems like SAP and enable fully automated plants to be controlled centrally. We have one client where the production planning team can launch batches from their desk with complex bills of materials downloading from SAP, materials being dispensed automatically, processed transferred from process to process automatically, changeovers between products are automated and the only human involvement occurs when the finished product is loaded on the delivery vehicle. However, this level of automation and control is very expensive and only viable for the largest manufacturing operations.
Manufacturing Execution System Tools
At the other end of the spectrum are off the shelf MES tools. Many of these are cloud based, which means that they don’t need to be installed on company servers or create security issues. One of our favourites is OFS. OFS has the advantage in that it can be set up entirely outside a company’s IT infrastructure and can even use its own sensors (a simple part counter) to track production throughput and downtime. This means it can be set up in as little as 15 minutes and start recording process data immediately. It can also be integrated to collect data from control systems, IoT sensors or ERP if required, but in the first instance, the part counter is often all that is needed to get an understanding of overall equipment effectiveness on the line
Another simple and effective tool is Team Assurance. This is a communication tool that allows issues to be easily recorded on a mobile device or on touch screens in the workplace along with photos or videos and then reviewed at daily meetings or escalated to functional support. It also allows for information to be communicated to teams directly and by requiring feedback ensures that issues are acknowledged and hopefully acted upon
A third option is MLean. MLean combines the capabilities of several tools and provides digital tools to support several elements of a Lean production system including 5S, TPM, Hoshin Kanri and Visual Management.
Like any software investment, the start point is to define what you want to achieve. Decide what features you must have and what would be nice to have and then evaluate a range of different solutions. Manufacturing industry exhibitions are a good place to look as multiple MES providers are present at most exhibitions these days.
Summary
To summarise, there are a growing range of manufacturing execution systems and data acquisition and analysis tools available to capture data from your process. These can be extremely useful in understanding operational performance and diagnosing problems in real time. The data is only valuable if action is taken as a result. Recognise that your front-line teams are the people that know your process best and can have the most influence on performance.
Therefore, make sure that the digital system does not disengage your front-line teams with a top-down approach. Consider retaining manual visual management in combination with digital tools in order to maintain this engagement and speed up response time to issues. Leader standard work and an Andon system can ensure that team leaders and managers take prompt action when your digital dashboards highlight problems. When selecting a software tool, be clear on what you want and what you really need. Keep it simple and consider ease and speed of implementation.
Finally, remember that software does not solve problems, people do. The best system in the world is of no value if people don’t take action when problems are highlighted.