The Merging of the Digital and Physical Is the Next Industrial Revolution
The next industrial revolution is bringing about untold change in every industry creating massive advantages and challenges to implement. Industry 4.0 will see the merging of physical & digital systems into a cyber physical system (CPS) that mirrors the digital realm in the physical world and the physical world in the digital realm.
What are the advantages of Implementing Industry 4.0?
In short, the advantages of Industry 4.0 include improved productivity and efficiency, better flexibility and agility, and increased profitability. Industry 4.0 also improves the customer experience by providing personalized products and services. In addition, Industry 4.0 helps companies to reduce their environmental impact by reducing waste and increasing resource efficiency. The adoption of Industry 4.0 is essential for companies to remain competitive in the global market.
Below we discuss more about the benefits of Industry 4.0:
Optimisation: Smart Manufacturing and Smart Factories bring with them optimizations and a growing ability to self-optimize production leading to nearly zero downtime of your machinery. Optimization will play a major role in keeping high end equipment maintained efficiently by having the right resources in the right place at the right time. Being able to utilize your production capacity constantly and consistently is better than a major down time or changeover.
Customisation: The interconnections of Smart Factories and the Industrial Internet of Things (IIOT) means your supply chain has shortened to a point where you must stay agile to customer demand. Communication between the customer and manufacturer will take place directly cutting out the need for manufacturers to communicate between departments internally or external providers. Smart Manufacturing allows easily scaling production up or down in relation to market demand.
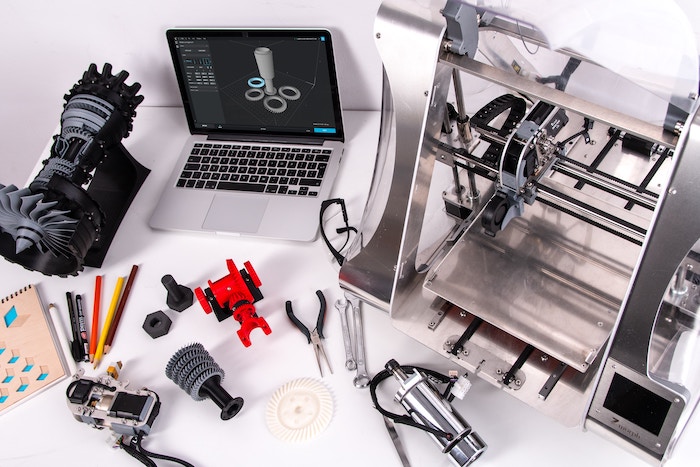
Reduce Costs: Implementing smart manufacturing may have a large initial up-front cost, but if setup correctly can have a positive impact on your bottom line with the implementation of automation, systems integration, data management, and artificial intelligence all having a major role in the profitability of your business.
Helping deliver these costs savings is an improved use of resources, faster manufacturing, less machine, and production line downtime, fewer quality issues, less material & product waste and lower operating costs.
Technology: Technology is progressing exponentially and having an increasing impact on our daily lives. Self-driving cars and augmented reality seem like science fiction, but these technologies are being used today in some capacity. Volvo has been testing autonomous trucks in a shipping port environment to collect data and view the interactions with the humans working alongside autonomous vehicles.
Microsoft has developed augmented reality glasses called HoloLens 2, used in a variety of applications but will shine in the maintenance & construction sectors. Technology advances will create untold opportunities for consumers and manufacturers looking to disrupt markets and find new ways of doing business.
What are the challenges of Implementing Industry 4.0?
Industry 4.0 is the current trend of automation and data exchange in manufacturing technologies. It includes cyber-physical systems, the Internet of Things, cloud computing and cognitive computing. Industry 4.0 creates what has been called a “smart factory”. Within the smart factory, cyber-physical systems monitor physical processes, create a virtual copy of the physical world and make decentralized decisions. Over time, the virtual and physical worlds will converge, and this process will accelerate with the increase of Internet of Things devices. The industry 4.0 concept developed in Germany and has since been adopted by many countries around the world. The goal of industry 4.0 is to create a more efficient and adaptive manufacturing process that can quickly respond to changes in demand.
However, implementing industry 4.0 comes with its own set of challenges. The results of a recent survey show that there are three main application fields that companies have been struggling with: simulation and calculation, automation as well as data management. Within these fields, there are common issues such as lack of software tools, design and production automation, data migration and collection, or data handling in production. These challenges need to be addressed in order for industry 4.0 to reach its full potential.
Below we discuss the top challenges of Industry 4.0:
Cybersecurity: The interconnection and digitization of systems is a key feature of i4.0 meaning there are more devices connected to the Internet of Things. This represents a massive cybersecurity challenge in terms of data protection and intellectual property. You will need to implement robust security systems to protect against hacking and unintentional data breaches.
Just like a chain, these connected cyber physical systems are only as strong as the weakest link. Policies, processes, and procedures should all be standardised to limit the amount of possible breach points in your systems.
Change Management: Embracing change is the secret to success for the majority of companies. i4.0 is changing the way we do things, merging the physical and digital together. These changes reveal a need to strategise ways to support your employees and empower them with the tools and skills needed to transition to i4.0.
Putting employees at the center of the change enables employee engagement at all stages, the human factor becomes a major lever for transitioning to i4.0. It is common for collaborators who are open to change to join the team as ‘change champions’ helping promote new technologies whilst helping colleagues adapt to new technologies.
Employment: i4.0 is changing the employment landscape with the need for employees to acquire different or all new skills to excel in these changing roles. Repetitive task workers will face challenges in keeping up with industry as their jobs are phased out or handled by an autonomous machine running 24/7. Education will need to transform to keep up with the demands of a rapidly changing labour market.
Capital Investment: i4.0 implementation will not be free, there will be varying degrees of cost involved from cheap IoT sensors used on existing machines or the purchase of large machinery with integrated i4.0 solutions. The capital investment needed for some of these larger projects might hurt the balance sheet in the short term but will have a multiplying effect in the long term by reducing your costs, increasing agility to market and customer satisfaction.
Do You Have an Implementation Strategy in Place?
Implementation of Industry 4.0 will cause major challenges in your business in the short term, but the advantages & benefits outweigh the challenges i4.0 will bring. You must start thinking about your Lean i4.0 strategy now or be left behind as more businesses take the leap to greater autonomy and disruption of traditional markets. TXM can help you understand where you are and where you need to be.
Implementing Industry 4.0 can be daunting, but careful planning can help ensure a smooth transition. First, it is important to understand the scope of your business and how it fits within the company’s broader strategy. Once you have a clear understanding of your goals, you can begin to prioritize your actions. Some areas to focus on include improving operational effectiveness, optimizing your value chain, and evaluating the possibility of creating new business models. By taking the time to properly plan and align your goals, you can make the transition to Industry 4.0 a success.