What is Project Manufacturing?
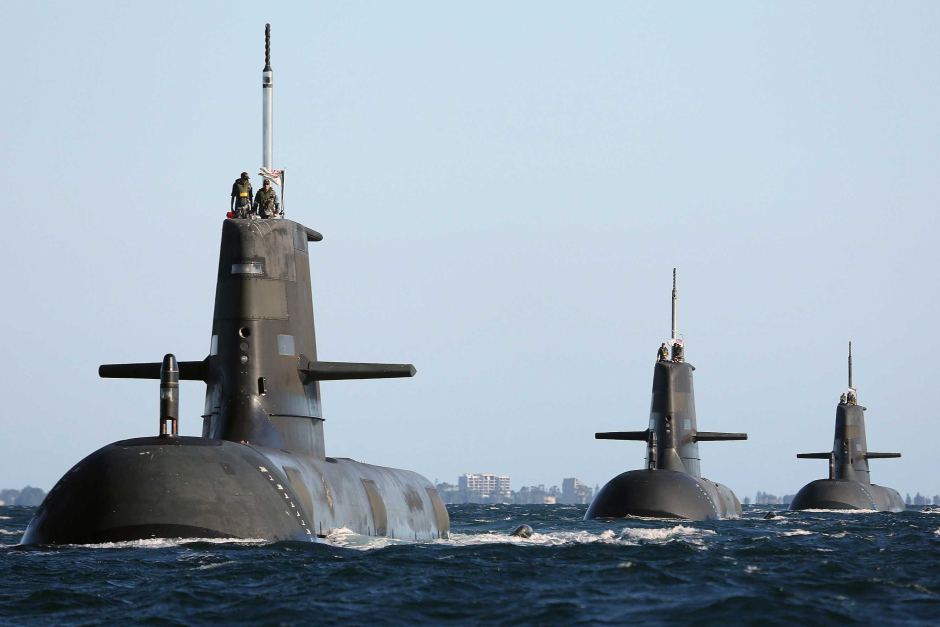
When we think of a manufacturing business, we usually think of a business that manufactures a defined range of products. These products are manufactured in the same way every time.
Product development typically involves a creative design phase, a process of testing and approval, prototyping or production trials and finally product launch. Much of our thinking and much manufacturing and supply chain literature assumes this model of manufacturing and product development.
Increasingly we see companies that operate in a different way. Their products are developed to meet a particular customer order. They don’t have a prototyping process because the product is a one-off. That is, every product is effectively a prototype.
They manufacture the product from some common parts on the shelf, but will also often require one-off bespoke parts. These parts are ordered just for that particular customer order. Finally, these products usually have a long lead time from order to delivery. Orders are often inter-related and sequenced over a period of time. I call this type of manufacturing project manufacturing.
Project manufacturing is not new, shipbuilding is a great example that has been around for hundreds of years. However, the major driver of the growth of project manufacturing is changing approaches to commercial and residential construction.
Globally the last 20 years have seen more and more of the elements of buildings manufactured off-site and delivered to the site. This approach makes sense as building sites tend to have limited space and the ability to control complex assembly processes and perform them efficiently is limited. Shifting elements of construction off-site simplifies on-site work.
“Manufacturing efficiencies” can be achieved in specialized factories dedicated to one element of the construction project.
The use of automated equipment greatly improves the efficiency of manufacturing and assembling elements such as joinery, structural steel or wall framing. This is much more efficient than doing this work manually on site. Examples of off-site construction include modular and relocatable buildings, pre-fabricated framing, structural steel, joinery, modular bathrooms, building maintenance cranes, HVAC systems, pre-fabricated building facades, and pre-cast concrete panels.
Project-based construction is also frequently seen in shipbuilding, plant and equipment manufacture, aircraft manufacture, commercial vehicle fit-out and heavy trailer manufacturing.
Seven Common Problems in Project Manufacturing and How to Overcome Them
Because of the unique nature of every product, project manufacturers often argue that they don’t operate a “production line” and that Lean does not apply to them. In fact, at TXM we have made something of a specialty over the years in working with project manufacturers. We see the same problems over and again. The seven most common problems we see in project manufacturing are:
1. Throwing Projects Over the Wall
For many project manufacturers, projects go through a series of handovers. Once the job is won, sales will hand over the project to engineering. Engineering will then complete the detailed design and hand over the designs and (hopefully) a bill of materials to purchasing.
Purchasing then order the parts and hand the job over to manufacturing. The problem with this approach is that no-one owns the whole project and that delays are allowed early in the project (often at customer instigation) that then compress lead times at the end of the project leading to expediting, escalating costs and late delivery. An effective project management function and end to end project management processes are essential to ensure that budgets and deadlines are met.
Learn Five Reasons Why You Spend Your Day Fire Fighting and What do Do About Them
2. A lack of standardisation and reliance on “ground up” customisation. Project manufactured products are inevitably one-offs, but that does not mean that they need to be completely bespoke in every way. Often engineers are allowed too much freedom to design every product in a unique way. Clear engineering standards, use of standard materials from a limited range of suppliers, standard sub-assemblies and customisation using “plug and play” options can greatly reduce cost, lead time, complexity and design risk.
3. Material shortages – Many project business spend their days expediting materials. Unfortunately expediting always leads to more expediting as pushing one order forward inevitably pushes other orders back. Kanban systems can be highly effective for standard items such as fasteners, fittings, common raw materials, and standard subassemblies. For bespoke parts, they need to be identified in the handover from sales, ordered as early as possible and then tracked by the project manager. Supplier lead times need to be respected and planned for.
Discover Five Ways to Improve the Performance of Your Suppliers
4. Incomplete and inaccurate information from sales and the customer: Products are usually highly complex in project manufacturing. It is reasonable for engineering to insist that information handed over on each new product is complete and accurate. Avoid the temptation to “just get started”, when information is incomplete as this rarely saves time and often leads to rework and errors. It is fair to expect that if customers fail to meet deadlines for providing information then delivery dates get pushed back accordingly.
5. Inadequate information provided to production: Too often production is expected to “just know” what to do when information on drawings and specifications is incomplete or inaccurate. This inevitably leads to errors and rework. Drawings need to be fully detailed and simple techniques such as colour coding can help prevent simple errors such as folding a part the wrong way or welding a cleat on the wrong side of a beam. A manufacturing engineering function can often greatly help the smooth transfer of information from engineering to production.
6. A lack of production “flow”: Project-based manufacturers often believe that they don’t have a flow. Products are manufactured in on place on the factory floor in what we call a “static build”. Workers often move from product to product based on availability of parts, “priorities” and, in some cases, worker preference. This approach is space-hungry, leads to long and unpredictable lead times, provides little indication of production progress and means that every tool and every material has to be transported to every job. On the other hand, creating a “pulse flow” where products move at prescribed intervals provides a visual indicator of progress and sets a real imperative to solve problems quickly so that products can keep moving. The result is usually shorter lead times, higher productivity and better use of factory space.
Learn how TXM Helped Boat Builder Sykes Racing to Create Flow Production in this Lean Case Study
7. Starting jobs that you can’t finish. Often the temptation can be to get a project into production, before you have all the parts, drawings and information. This is fraught with risk. Instead, develop a “good to go” process where jobs are only released to the line if all the parts and documentation is ready. If project managers see that the production “timeslots” are approaching, it tends to focus their mind to make sure that everything is delivered on time and that their project is “good to go” and does not miss its scheduled production time slot.
Summary
Project manufacturing is a growing phenomenon, especially in construction. It is true that this type of manufacturing requires a different approach to traditional manufacturing. However, if the benefits of project manufacturing are to be truly delivered then Lean thinking needs to be applied in a targeted way to ensure that project manufactured products are always delivered on time, on quality and on budget.