Client PVC floor manufacturer
Location Changshu, China
The Challenge
Our client is a global leading indoor PVC floor manufacturer. The reliability of the equipment is critical in the process industry. Our client had established a good foundation for maintenance, however, the Changshu plant realised that it was not enough to achieve high reliability as dust in the production area was a critical environment and health issue. Our client expected a systematic TPM program to change the culture of equipment maintenance.
The TXM Solutions
TXM supported the Our client plant to implement three pillars of TPM, these included: Autonomous Maintenance, Planned Maintenance and Focused Improvement. The main actions implemented at our client’s Changshu plant were:
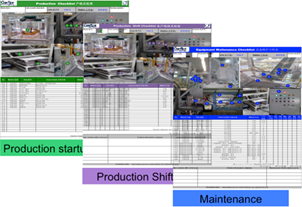
- Using the TXM 7 abnormalities detection List, operators and maintenance workers found more than one hundred abnormal items, including minor defects, lack of basic conditions, areas hard to reach, sources of contamination, quality defect sources, unnecessary items and safety defects.
- Establishing equipment cleaning and checklist at critical machines so the operators could find out the abnormalities of the equipment before the whole production line breakdown. Equipment was “visualised” in order to make inspection easier.
- FMEA was used to evaluate the failure mode of parts of equipment in order to establish PM (planned maintenance) program and spare parts system.
- Special focused improvement teams were set up to tackle difficult problems or repeated problems.
“Zero Dust” project was established to solve the dust environment and health issues. A feeding system was sealed to prevent dust leakage in the production process rather than spend a lot of time on cleaning it every day.
The Results
- After 5 months of implementing the TPM program, achievements include:
- Establishing an Autonomous Maintenance system. Operators check and clean the key equipment in every shift, find abnormalities in advance and extend the life of equipment;
- Finding more than 180 abnormalities of equipment were resolved during the project period;
- Developing a visual representation of equipment which has made inspection easier for operators;
- Incorporating a “zero dust” state was developed and the shop floor environment was also improved this improved employees’ health and satisfaction;
- A planned maintenance and spare parts system was established.