Client Houston's Farms
Location Hobart, Australia
Houston’s Farms Lean Agribusiness Case Study
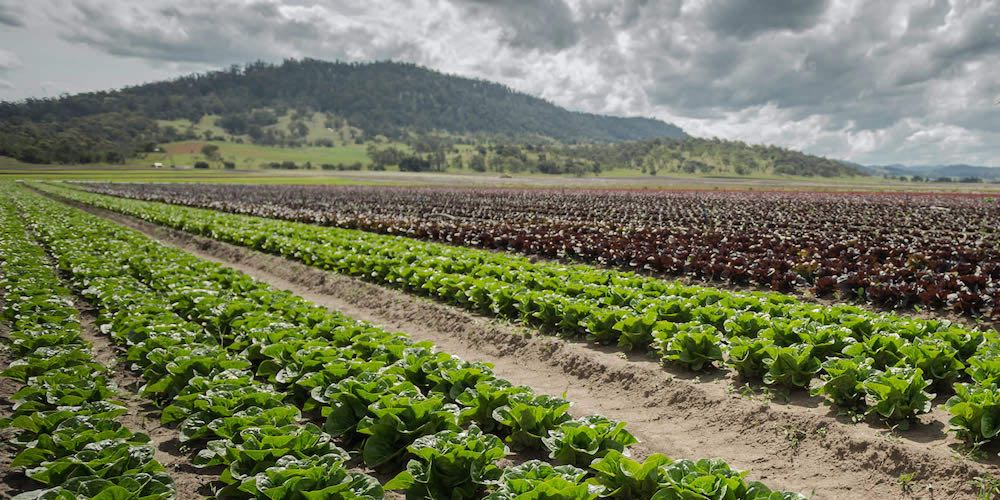
This case study involved pioneering the application of Lean manufacturing concepts to the end to end process of fresh vegetable production from sowing to shipping.
Our customer is a large commercial grower and processor of fresh cut leaf vegetables for pre-packed salad. They farm over 1000 hectares of fancy lettuces and herbs and operates processing plants in Hobart and in Brisbane. Our customer has a market-leading reputation for quality.
Fresh leaf vegetables such as lettuce have an extremely short shelf life. The challenge is increased by the location in Tasmania. This requires product to be shipped daily to the Australian mainland. The location also places our customer at a serious disadvantage to its mainland competitors. As the market for pre-packed salad has matured, they have recognised the need to reduce unit costs through improved productivity and reduced waste throughout the supply chain from sowing to delivery to the customer distribution centre.
The TXM Lean Solution
TXM mapped the end-to-end process of producing pre-packed salads from receipt of seeds and seedlings through to delivery of finished product to mainland customers. This highlighted key areas of waste and provided a roadmap for improvement.
TXM then focused on coaching improvement in the two processing plants and farm. The initial focus was on the packing process to improve organisation, using 5S and to improve filling and packaging uptime and productivity using standard work and problem solving. Standard methods were developed to pack product, while packing line layout and finished product staging was improved and key causes of filling machine downtime were addressed.
Initial focus in the farm was on harvesting as the lack of a standard method for harvesting had led to inconsistent levels of productivity and quality. Additionally, poor organisation of product pick up led to product degradation and loss when it was left in the fields for too long. Standard work for harvesting and product transport was developed to ensure that a consistent result was achieved with optimum productivity.
Sowing and growing was also the focus of improvement with the 5S approach adapted to ensure that routine crop checking and irrigation was carried out correctly.
The supply chain was the final area of improvement with Lean approaches being used to improve planning in order to reduce waste (dumping or destruction of unwanted crops) and the need to transport crops around Australia in order to balance demand.
The Results
On time delivery has been increased to 100% and maintained at that level for several months. This is critical as missed deliveries usually end up being scrapped due to their limited shelf life.
A productivity improvement of around 20% has already been achieved in filling and packaging through better layout and reduced downtime. This has also lead to substantial savings in rework and wasted packaging.
On the farm, gains have been made in harvesting productivity and focus is on improving yields through standardisation to ensure compliance with optimum processes for sowing and irrigation.