Client BPH Attachements
Location Billingshurst, UK
Background
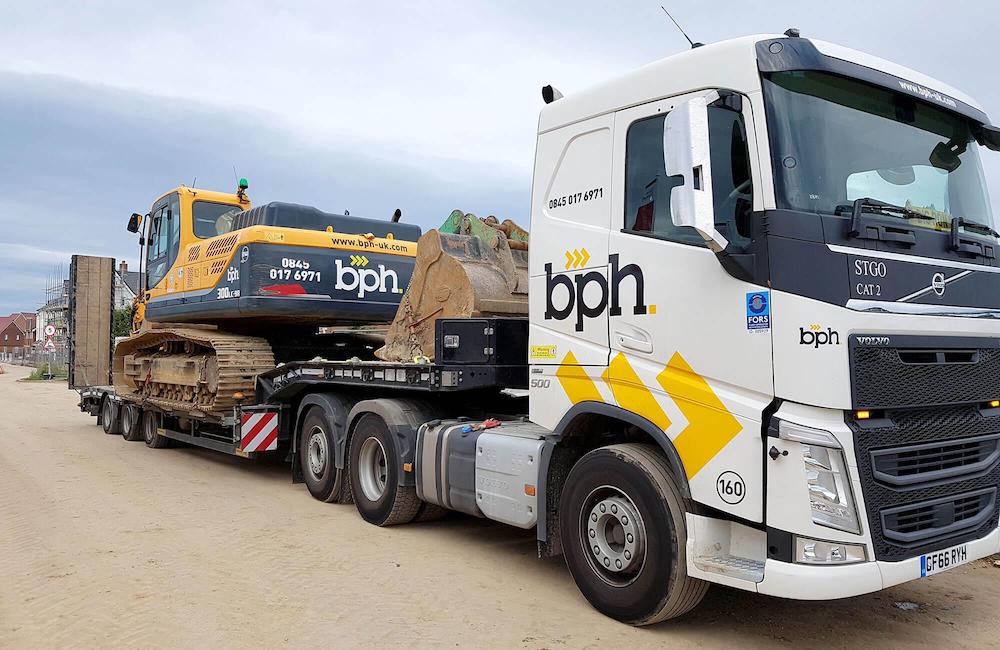
TXM were appointed in 2022 to review the operations at BPH Attachments and to help them to improve the flow of information and product throughout the business. BPH Attachments are based in Billingshurst, Sussex. They are UK’s most respected supplier of high-quality hydraulic excavator attachments. There are four main aspects to BPH Attachments: the sale of new and used excavator attachments, UK-wide hire (with over 550 attachments in their rental fleet), repairs of all brands of hydraulic attachments and they also hold an extensive stock of PRODEM parts.
BPH Attachments have a wide range of excavator attachments which enables them to be able to serve customers across construction, demolition, scrap metal, recycling, road contractors, utility contractors, housebuilders, machinery dealers and plant hire. BPH Attachments operate from an on-site workshop. This workshop is run by a skilled team who keep the fleet of machines and operations ready for use. This workshop also fabricates brackets and fixtures to ensure attachments fit the base machine correctly.
The Challenge
BPH Attachments’ objective was to improve their business systems and processes. The goal was to streamline and optimise the sales order fulfillment and production steps from order entry though manufacturing to despatch, and to drive up productivity and reduce lead time.
BPH needed to increase the pace of production, through the introduction of effective visual management, such as daily KPI’s and metrics based on customer demand. This approach would enable production to meet and exceed current demand in line with growth expectations. It was also important for the performance against schedule to be transparent to management at any time during the day.
Finally BPH also needed to optimise the stock profile and inventory levels to maximise the use of space and deliver materials efficiently to production by improving stock accuracy, stock location and handling.
The Solution
In order to develop improved systems, TXM Senior Consultant Tim Scurlock, facilitated a series of workshops with cross-functional team at BPH using Facility Layout method called the TXM Facility Layout Development Process (FDLP™) and TXM Manufacturing Agility Process®. The team mapped the end-to-end information and product flow through the business. They identified metrics and measures on the way which would help sustain the implementation.
Ten core processes were mapped within the business. This ranged from the Sales Order, Receipt Process, to Part Order, to Delivery Processes, from On-hire and Off-hire process through to the purchase ledger and approval process. Workshops were conducted over a period of 12 months addressing these core processes. “We worked with the users of each process, which included defining process steps, identifying pinch-points, and problems, before streamlining and standardising the future state” says Tim Scurlock.
Tim then worked with the BPH team to implement a wide range of improvements that were identified in the workshops. This included changes to improve the control of materials so that the right part was always in the right place at the right time. Stock accuracy has been achieved with better organisation of parts, clear accountabilities and cyclic stock counts.
A Kanban system was established to ensure that standard brackets were always available when needed. Critically there was a focus on improving the flow of information between sales, operations and the invoicing teams. A standard toolkit for each service van was introduced to make sure that technicians always had what they need on site to get the job done.
The Results
|
|
Standardised stock locations and codes | Kanban system in place for Attachment brackets |
The results are very visible says Tim Scurlock, there’s a new site which is clean, tidy and well organised as well as calm. Together all the changes had the effect of promoting the idea that the information flow from Sales through to Invoicing is a series of processes that need to work well together, with internal suppliers and customers at each stage. This has resulted in better teamwork, fewer hassles and better results for customers.
Matthew Bastable, Director at BPH is very pleased with the results. He says “the cultural change in the teams over the past 18 months is tangible. Our business now is process led and there’s a respect between teams and a ‘will to win’ attitude towards getting the processes right”.
TXM Lean Solutions are a global operational excellence consultancy with offices across the United Kingdom, Europe, Australia, North America & China. Need help streamlining your business? Contact TXM today!