In every manufacturing process, our aim is to add value to a product that the customer will pay for. While adding value to our products, there are tasks that must be done to complete the work but don’t directly add value; set-ups and inspection, to name a few. Then there are the other activities that occur during production that are waste.
According to Lean Manufacturing principles, waste is anything that creates no value that the customer is willing to pay for. Waste is defined in terms of value therefore we can only know the waste by first knowing the value first. Waste, therefore, is relative to the customers’ needs.
How Do We Begin to “See” the Waste in Our Production Systems?
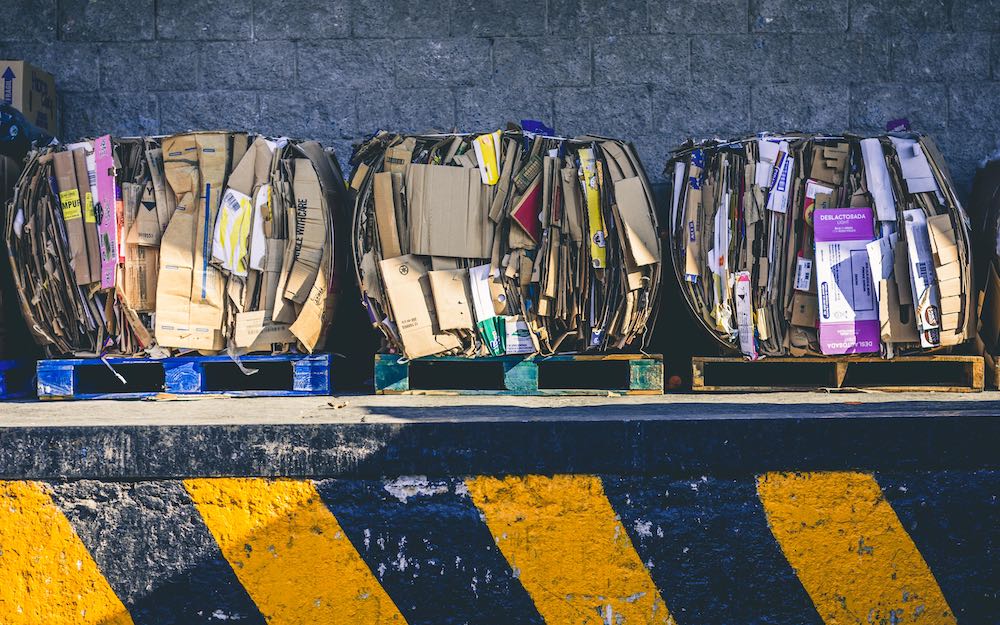
We begin to investigate the value-adding steps and cycle times in our process, through a Value Stream Mapping process. Out of this process, we now understand how long the value-adding steps take and the overall lead time it takes to get a part all the way through to the customer.
We realise that there is always a BIG difference between these two times. The difference between value-adding time and the lead-time time provides us with the opportunity to remove the hidden wastes in the value stream. The difference in times is where we can begin to focus on and discover where wastes are hidden.
The 7 Wastes
The 7 wastes (or Muda) have been defined by Taiichi Ohno, the father of the Toyota Production System, and they have become known as the 7Ws.
The original seven Muda (Wastes) are:
- Transport (moving products that are not actually required to perform the processing)
- Inventory (all components, work in progress and the finished product not being processed)
- Motion (people or equipment moving or walking more than is required to perform the processing)
- Waiting (waiting for the next production step)
- Overproduction (production ahead of demand)
- Over Processing (resulting from poor tool or product design creating activity)
- Defects (the effort involved in inspecting for and fixing defects)
In order to remind us of these concepts, Acronyms can be a very effective tool and here a few examples,
An easy way to remember the 7 wastes is TIMWOOD
T: Transportation
I: Inventory
M: Motion
W: Wait
O: Over-processing
O: Over-production/Excess-processing
D: Defects
Another easy way is NOW TIME: It’s now time to eliminate Mudas:
N: Non-Quality
O: Over-production
W: Wait
T: Transportation
I: Inventory
M: Motion
E: Excess-processing
With the 8 wastes use the acronym DOWNTIME is a useful memory aid.
D: Defects
O: Over-production
W: Waiting
N: Non-utilized Human Resources/Talent
T: Transportation
I: Inventory
M: Motion
E: Excess Processing
*Note this has now been expanded to include an eighth waste of “Non-utilized Human Resources/Talent”.
What are the 8 Wastes?
Defects
The simplest form of waste is components or products that do not meet the specification.
The Toyota quality achievement came with the switch from Quality Control to Quality Assurance – efforts devoted to getting the process right, rather than inspecting the results.
Over-Production
A key element of JIT was making only the quantity required of any component or product.
This is the main challenging point to the Western premise of the Economic Order Quantity (EOQ) upon which MRP system is built on. This defines the fixed ordering costs, built around set-up times, and thus the need to spread these fixed costs over large batches. The Toyota production system moved from long set-ups to Single Minute Exchange of Die (or SMED).
Waiting
Time that is not being used effectively can only be a waste – we are incurring the cost of wages and all the fixed costs of rent, rates, lighting, and heating so we should use every minute of every day productively.
The Toyota production system is focused on the reasons why machines or operators are under-utilised and set about addressing them all. Thus we have new tools for preventive maintenance, the creation of flow and the emphasis on takt time.
Transportation Waste
Moving items between areas, buildings or factories incurs a cost, in energy to initiate the movement – such as the petrol absorbed by a forklift truck. However, there is much more than just the accounting costs; the movement brings other costs. Managing a factory with operations spread apart is much more difficult than when the subsequent stages are located in the same work cell adjacent to one another.
Excessive Movement
Separate from the transporting of items is movement. People spending time moving around the plant or cell is equally wasteful.
The time a machine operator wastes walking around in order to find a piece of tooling or spanner could be better utilised if we improve housekeeping by locating every needed in a place that is close at hand.
Over Processing
A good example from my own experience relates to surface finishes requirements on the component. The original drawing required a cyclonical grinding to improve the surface finish after turning. When a new CNC machine was installed the required surface finishes could now be achieved with a finished path of the new lathe.
Thus the grinding operation was removed. A basic principle of the TPS is doing only what is needed.
Excess Inventory
Now everyone understands that a key element of the Toyota production system is that a JIT production system reduces the cost of inventory. By lowering the inventory we can then see the problems in resupplying the inventory in short lead times.
Thus lean is a continual process of improvement.
The eighth waste – Non-utilized Human Resources/Talent
The waste of not using people to the best of their unique abilities. How can we involve everyone in developing ideas to generate improvements and new products?
Now you have an understanding of the 8 Wastes and how to identify them you can start to learn about Value Stream Maps and how to create your own Value Stream Maps to identify where the wastes in your processes.
Value Stream Mapping sessions are some of the most powerful Lean tools you can use to enhance your business, it’s people and process.
7 Lean Manufacturing Wastes and How to Get Rid of Them
Business processes can either create waste or add value when goods are produced. Wastes do not bring any product value, and it’s therefore vital to eliminate them.
If you don’t remove the waste, it’ll lead to increased costs, lower employee satisfaction, lower profitability, and decreased quality.
Lean production highlights things that add value while reducing waste.
7 wastes examples
Here are the examples of the seven wastes:
-
Transportation
Transportation is the movement of products from one point to another. However, it does not add any product value. Transportation is a waste since products don’t need processing and are also at risk of being damaged. Transportation waste is caused by large batch sizes, several storage locations, and complex production processes.
-
Defects
Any defective item needs replacement or repair, which leads to wastage of resources. It is caused by human errors, poor communication, lack of standardisation, inadequate quality control, and insufficient machinery repair.
-
Inventory
Inventories refer to finished products and works in process. Any raw material that is not being sold is a cost to a business. The causes of inventory waste are overspending on inputs, inventory defects, and overproduction of goods.
-
Motion
Motion waste includes the movement of operators and equipment not done in a simple way. It can be people walking more than required. Motion waste includes lifting heavy things, non-ergonomic office layouts, and walking to deliver paperwork.
-
Over-production
Over-production is producing more than is needed and can lead to excess inventory. Some of its causes are poor automation, poor forecast of demand, and unpredictable production schedules.
-
Waiting
Waiting is also known as queuing, and it involves dealing with any interruptions in production when there is a shift change. It is caused by bottlenecks, poor process planning, and unplanned downtimes.
-
Over-processing
Over-processing is where a lot is put into a product that does not add any usefulness to the customer. It is caused by the use of outdated methods, unnecessary production steps, a slow approval process, and a lack of standardisation.
How do I get rid of 7 wastes?
You can eliminate the 7 wastes by using the following steps:
- Make waste visible
- Be conscious of the waste
- Be accountable for the waste
- Measure the waste
- Eliminate the waste
How to optimise resources with waste management
You can optimise resources to avoid any wasteful activities by doing the following:
- Improving quality control
- Reviewing processes
- Creating documentation
- Apply automation to increase accuracy
- Balancing workloads
- Reducing set-up times
- Good communication
- Planning office layouts to maximise efficiency
- Keeping things simple