How do we approach Waste elimination in a manufacturing environment?
Start by developing a structured process that is simple and centred on reducing the waste, no matter how small, as this will add up over time to build team skills and improve performance. It is better to do something small rather than not addressing the wastes at all.
In any manufacturing processes, the wastes are not easily seen at a first glance, and the task of identifying then requires a structured approach to eliminate wastes.
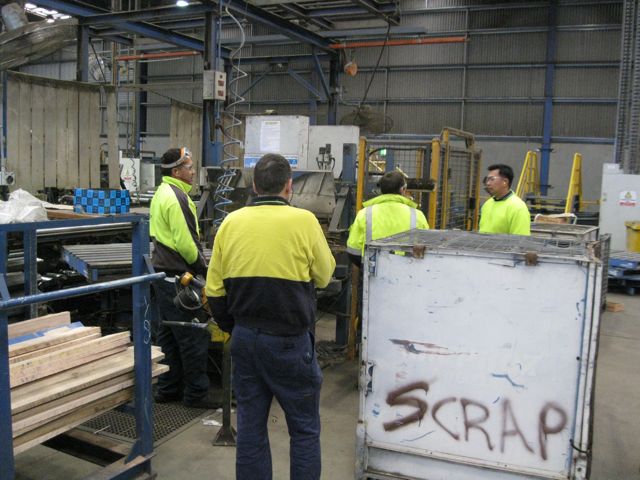
How To See Waste
How do we begin to “See” the waste in our production systems?
Before beginning on our Lean journey, as long are people look busy and the machines are always running, then we thought things were good. Once we begin to investigate the value-added steps and cycle times in our process, through a Value Stream Map, and compare this with the overall lead time it takes to get a part all the way through to completion, we realise that there is a BIG difference.
And this big difference in times is where we can begin to focus on and discover the waste that’s hidden.
In traditional manufacturing, waste isn’t always obvious. It’s like the bubbling stream on the left; looks lovely – it’s full of inventory. Some parts will wander to the left, others will get stuck.
The problems are hidden.
Lots of inventory often means lots of double handling, as we have to shuffle it around. Quality problems are hidden and rework levels are high. Over-processing or overproducing parts is a simple part of the way we work. And trying to find anything?!? Well, good luck!
A Structured Way to Eliminate Wastes
Creating a structure is more work than just talking about eliminating waste and expecting people to “do it”. This structure needs to allow people to identify and report wastes that they find within their day to day tasks. Then to support them with the resources to go about reducing and eliminating the wastes. By creating a structured process and linking this to the daily routine can help to develop a repeatable process that builds upon itself towards a Waste Reduction Culture.
To move towards a waste reduction culture, it is difficult to get employees to offer up ideas or suggestions to improve their performance by removing wastes from a set process or their own work tasks. Many companies had tried to implement a “suggestion box” with varying levels of success but these tend to not be effective or are short-lived in providing beneficial returns.
The problem with the suggestion box approach is that the suggestions are usually aimed at “somebody else” in the company to fix. When one of the ideas is not implemented, or there is a lack of feedback about its status, most employees tend to stop suggesting improvement ideas. Ownership in the process is missing and it is difficult to develop any structure from these random suggestions.
A waste reduction culture starts with giving all employees the skills to contribute at their level. There is a place for the bigger picture projects that may be recommended by internal specialists or consultants however these are typically more sophisticated and need analysis and larger amounts of time to implement, such as in new processes or new machinery.
How To Reduce Wastes
Start by providing practical skills and know-how to all employees, so that every employee can develop their own suggestions which can be easily and rapidly be implemented.
These teachings are a knowledge bank of waste identification, using The 7 Wastes and the practical skills to be able to observe work that develops improvement ideas.
With these two teachings, the ability to identify an improvement becomes easier. This is then followed by the opportunity to implement a possible solution. Small amounts of time are needed to allow individuals and teams to set a regular time for offering, discussing, and most importantly, implementing and trialing ideas.
By having time to shared ideas and to work at implementing them, it becomes a critical part of developing ownership. Often the first improvement itself is less important than the improvements that might spin out from implementing an idea. This is how Waste Reduction starts and repeating it many times over will create a new culture of waste reduction.
The time may be a little as five minutes a day and be included as part of the Daily Team Meeting. Basic problem-solving tools can be used to assist our teams to work through ideas, including a flip chart or whiteboard, Before and After pictures, Waste walk sheets, and Observation sheets.
Get Started!
Having a structured approach to waste elimination will start the ball rolling, where many small suggestions are being rapidly implemented and achievements are being gained. These all add up to contributing towards improved performance and a culture of waste elimination as the norm.
Contact us to learn more