What is the production capacity of your business?
It is surprising how few manufacturers can answer this question.
Even for those who can provide an answer, it is likely to be inaccurate.
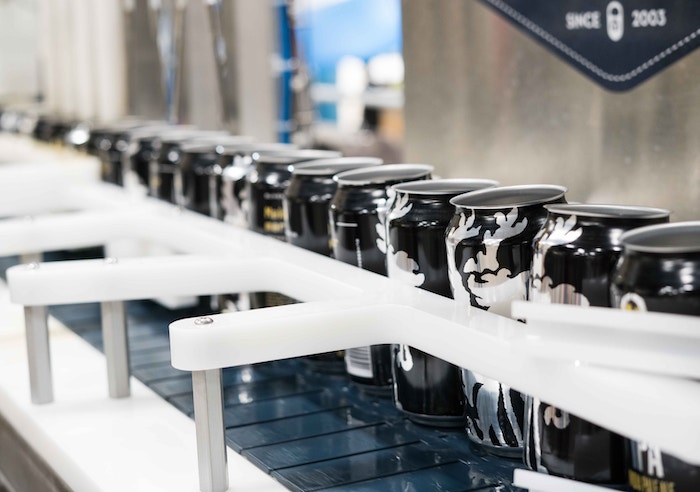
Why Does Understanding Production Capacity Matter?
Many business decisions are based on assumptions about the production capacity of your business.
For example, your decisions to purchase new equipment, take on new business, add another shift or relocate your business will all be based on your actual or perceived level of capacity. The consequences of not understanding capacity can, therefore, be very serious.
You might take on business you can not service, purchase equipment you don’t really need or take on a building that is too large.
How Do You Measure Production Capacity?
There are many ways to look at production capacity in your business. In planning for sales growth you need to consider “demonstrated capacity”. That is the actual rate of output that has been achieved in recent history, allowing for inefficiency.
This ensures that if efficiency does not improve your customers will still get their product on time. Of course when efficiency improves you may be able to get ahead of demand. In this case, your increased “demonstrated capacity” will provide further opportunity to grow sales.
When considering investments evaluate “nameplate” capacity to determine the hidden potential of your assets due to inefficiency. If efficiency is poor then focus on improving it through reducing set up time, downtime and defective product. This will provide much better returns for your business than investing in new equipment. Capacity changes over time as you add machinery or improve efficiency.
Therefore you need to regularly review your capacity and compares this to your future demand for products. This capacity review usually forms part of your Sales and Operations Planning process.
Consider the Whole Chain When Calculating Production Capacity
For a multi-step process, your production capacity will be limited by the slowest step in that process, the constraint. At TXM we like to look along the entire production process (or “Value Stream”) from supply of raw materials to shipping of finished goods and all the steps in between.
We compare each step in this process to a common yardstick called Takt Time, or the rate of customer demand.
So if we sell eight units per day from our factory and operate one, eight hour shift our takt time is one hour.
Therefore every step in the production process needs to be able to produce at least one unit per hour.
A simple bar graph (called a line balance chart) can compare the actual output of each production step (cycle time) with takt time and quickly highlight bottlenecks.
Take Into Account Human as Well as Machine Capacity
There may be many steps where the rate of production is determined by people and not machines.
In this case, you need to know the normal rate of production for these processes. “Standard Work” is an excellent process for achieving a consistent output and eliminating waste and inefficiency in processes where people set the pace.
People can also be a constraint even when they don’t work on the production line. At one company I recently spoke to, capacity is limited by the ability of administration and engineering staff to process customer orders and design data.
This can be hard to measure, but the consequences of overloading these functions will be just as devastating for customer service as a bottleneck in production. Standard work and value stream mapping can help identify and improve office capacity constraints. Understanding your capacity is vital to managing a successful manufacturing business. We can assist you to understand and increase the capacity of your business.
Common Questions On Production Capacity
How to measure production capacity?
Lean Manufacturing is all about making small, incremental changes that add up to big improvements in productivity. And one of the best ways to measure the impact of Lean Manufacturing is to track production capacity. There are a few different ways to measure and hopefully increase production capacity. The most common is through Utilization, which measures the percentage of time that a machine or process is actually in use. For example, if a machine is in use for 8 hours out of a 10-hour shift, its utilization would be 80%.
Another way to measure production capacity is OEE, or Overall Equipment Effectiveness.
This metric takes into account factors like downtime, quality issues, and setup time, in addition to utilization. No matter how you measure it, monitoring production capacity is a crucial part of Lean Manufacturing. By tracking this metric, you can identify areas where your process is inefficient and implement changes to improve productivity.
How to calculate production capacity formula?
In Lean Manufacturing, one of the key metrics that is tracked is production capacity. The goal is to minimize waste and produce only what is needed, when it is needed.
To calculate production capacity, you need to know three things: the Takt time, the Cycle time, and the number of machines.
The Takt time is the paced time required to produce one unit of product.
The Cycle time is the actual time it takes to produce one unit of product.
The number of machines is the number of workers required to produce one unit of product.
To calculate production capacity, you need to divide the Takt time by the Cycle time. This will give you the number of units that can be produced in an hour.
To calculate the capacity for a day, you need to multiply this by 8 (for 8 hours in a work day).
Finally, to calculate the capacity for a month, you need to multiply this by 21 (for an average of 21 work days in a month). By understanding and tracking production capacity, Lean Manufacturing helps companies stay efficient and produce only what is needed.
What is Production Capacity?
Production capacity is the maximum amount of output that a company can produce using its current resources.
The concept of production capacity is central to Lean Manufacturing, which is a methodology used to minimize waste and optimize manufacturing efficiency.
Lean Manufacturing principles are based on the belief that all manufacturing activities should add value for the customer and that any activity that does not add value should be eliminated. By maximizing production capacity, Lean Manufacturing helps companies to reduce waste, improve quality, and increase customer satisfaction.
In short, production capacity is a key metric for manufacturing success.