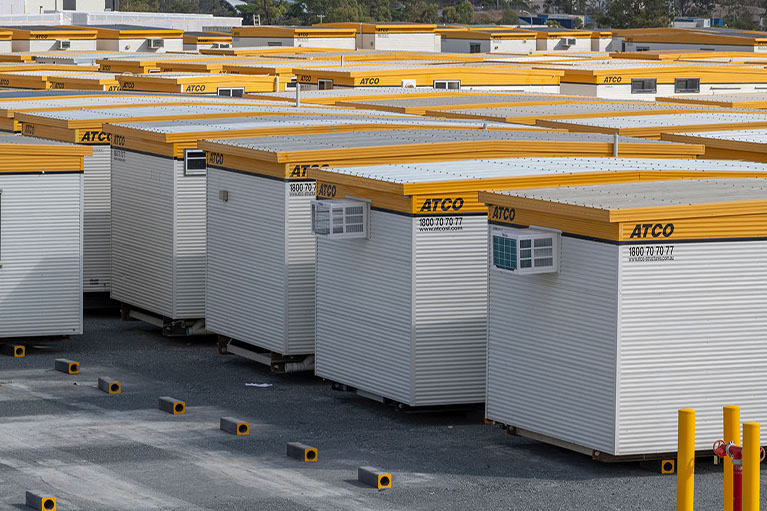
Manufactured or modular housing gets a lot of hype. For years it has been heralded as the future of building and modular housing start-ups seem to spring up in the media every day. Over the years we have worked with a wide range of modular builders and have learned lessons about the potential and the limitations of this approach.
While I will mainly refer to housing in this article, the modular approach can be applied to education buildings, offices, and a range of other building types. It can also be applied to elements of the building such as modular bathrooms. The problems and solutions I outline below apply to all types of building.
The Fundamental Disadvantage of Modular Building
The potential benefits of manufactured modular housing get hyped so much that often the very clear disadvantages of this approach to construction get ignored. Modular houses are manufactured in a factory (or sometimes out in a yard) at a site located some distance from the final location of the house.
This means that the house needs to be transported from the factory to the house location, adding cost and complexity and imposing design limitations on the building. The house needs to be designed so that it can be assembled from one or more modules that can be sized to fit on a truck and travel on public roads.
To move the modules safely they need to be built on sturdy base, which is usually manufactured from structural steel or timber and the overall structure of the building needs to be strong enough to handle the shaking that may go on in transit. All this adds cost and then you have the obvious cost of the actual transport to site and cranes to load and unload the modules at either end of the trip.
So Why Bother with Modular Housing?
Given this large competitive disadvantage, one might wonder why anyone would even bother with modular housing. However, as I said at the start of this article, modular builders are proliferating everywhere. This is because modular housing can offer some real advantages over on-site construction that can offset the costs and limitations imposed by transport.
The Advantages
The most important advantage of manufactured off site construction is the ability to complete the construction work in a controlled factory environment and to create manufacturing efficiencies in the production process. Done well, this can deliver lower labour costs, less material waste, and dramatically shorter construction lead times.
Another big advantage for rural homes and holiday houses in remote locations is that modular building enables trades work to be centred at one location rather than tradespeople having to travel to every single house. The key is to stop thinking like a builder and start thinking like a manufacturer.
Simplification and Standardisation Is the Key to Low Cost
Everyone likes their home to be unique, but for modular builders the more the design can be simplified and standardised the greater the benefits of the modular approach. This is not all that different from what high-volume on-site builders do where buyers select from a range of standard designs and customisation options to configure their home. Some modular builders have even developed website tools that enable potential homebuyers to “design their own home” online, such as this New Zealand builder Genius Homes.
A standardised approach can limit the range of materials and finishes that you need to handle and allow you to standardise the construction method and construction times. This also means that the manufactured housing approach is most effective in smaller and lower cost buildings. The larger, more complex, and more bespoke the house becomes the fewer the advantages from building off-site.
Lead Time Is Key
One of the fundamental goals of Lean thinking is reducing lead time and for modular home builders this is the message of maximum importance. Reducing construction lead time from starting the base to installing the home on site has multiple benefits. Firstly, it means that the customer gets their home sooner and this can tip customers in the direction of a modular home.
Secondly it means that investment in materials and labour gets turned in to cash faster, reducing working capital and strengthening the balance sheet of the business. Finally, the shorter the lead time, the fewer houses need to be in construction at any one time, thereby increasing the capacity of a factory space.
For example, a typical medium sized modular builder of low-cost housing might manufacture 200 modules per year of an average size of 60m2. This relates to an average production rate of around four modules per week.
If the lead time to produce a module is 12 weeks, then the builder will have 48 modules in progress. If we assume that 150m2 of workspace is needed for a 60m2 module then 7,200m2 of workspace plus storage = 10,000m2 is needed to accommodate all the homes in various stages of completion.
If the work is to be done under cover, then an investment of around $15-$20m is needed to construct a building of that size (or rent of around $1m per year). However, if the lead time for construction was four weeks, then the number of homes in progress would be 16 and space needed just 3,500m2.
How to Reduce the Lead Time
If you are finding the idea of building a home in four weeks hard to comprehend, you probably won’t believe me when I tell you that the team at TXM has reduced the lead time for some modular buildings to four days.
The key to reducing lead time is eliminating non-value-added time. Take some time to observe the workers on your site. Of the houses in progress, how many are being worked on at that moment? Of the workers you see, how many are engaged in a task that adds value to the building as opposed to one of the eight wastes?
You will probably find that at any given point in time that several of the houses in construction on your site are not being worked on. The challenge is then to find out why. Usually, the reason is that the building is waiting for materials. Therefore, a key focus of your operation needs to be developing supply chain processes that ensure that the right materials reach the right house at the right time to enable work to continue uninterrupted.
Once you have the supply chain functioning, eliminating non-value-added work is the next challenge. The best way to eliminate waste is create what we call one piece flow. Most builders use what we call a “static build” approach. That is, a base frame is placed in a location in the factory (or the yard) and the house is completely constructed at that location. Materials and workers must be brought to the house.
The alternative to this an approach sounds fanciful but is used by a significant number of modular builders. That is, the house moves to the workers and the materials. What I am talking about is effectively a house assembly line, where the complete building or building modules move through a series of workstations from the initial base to completion.
More than just believing that this approach is feasible, I believe that modular builders will only achieve the true benefits of the manufactured approach when they adopt one piece flow. In fact, every static build operation I have ever seen ends up being a version of on-site construction with the added cost of relocating the building to site.
Creating The Flow
Creating one piece flow requires a detailed understanding of the steps of construction, the time involved in each step and the materials and tools required at each location. From this you can work out how many workstations are needed and what needs to happen at each workstation.
By moving the building through a series of workstations, the activities at each location can be specialised, so one might focus on frame building and floors, the next on first fit for electrical and plumbing, the next on cladding and roofing and the next on wall linings etc. This means that only the materials, tools and specialised staff needed for that workstation are needed and they can be located and replenished permanently at that location, eliminating the need to move materials to the job.
Not every task needs to happen on the production line. It can make sense to “modularise the submodules”. For example, assembly of building frames, joinery, preparation of materials and even some plumbing and electrical work can be done offline and brought to the line as needed.
A Different Approach to Labour
On site builders typically rely on a range of subcontractors to complete the construction. This helps the builder manage risk as they only pay for the subcontractor when they are on site. Builders often negotiate a fixed price or a “per building” or “per square metre” rate with their subcontractors. Many modular builders extend this approach to their operations. This is usually a sign that they are still thinking like a builder, not a manufacturer.
In a true manufacturing environment, you need a constant rate of production all day every day. You cannot afford to have a building stuck on the production line because the subcontract plumber you usually use is held up on another job.
Therefore, you need a stable, constant workforce. This usually means directly employing staff. There may still be a need for some flexible temporary labour to handle peaks and troughs of workload, but the core of the team needs to be your people. This does add some risk, but also means that the per hour rate that you must pay for your staff is greatly reduced.
Per job and per square metre payment rates are also problematic. Firstly, they encourage a focus on output rather than quality which can lead to defects that get found later in the process. Secondly, they can often introduce imbalances into the flow where, for example a plumber may look to “get ahead” and complete work out of sequence, causing issues for other trades or causing material shortages.
Payment of staff per hour does require clear measures of daily output and greater supervision, but ultimately allows for greater control of the production process. A “one piece flow” approach that requires the building to move to the next workstation at a fixed interval also enforces a level of productivity as each workstation must complete their work to meet the rate of the line.
It is important to remember that much (if not the majority) of work in a building does not require a fully qualified trades person. Tasks such as assembling prefabricated frames, assembling, and installing joinery and attaching cladding or wall linings can be completed by semi-skilled factory operators.
By standardising this work and doing it in a controlled “factory” environment an equal or better result can be achieved than if it were left up to tradespeople to do it their own way. Qualified tradespeople can then be reserved for tasks where regulations or the nature of the work require it such as plumbing or electrical fit off.
Flat Packs Vs Modules
One of the key questions I see being considered by modular building start-ups is whether to manufacture whole building modules that are difficult to handle and transport to site or to produce a panel solution that can be shipped flat and then assembled on site. While there are obvious transport cost and handling benefits of the flat pack approach, I think these are far outweighed by the disadvantages.
The flat pack approach leaves too much work to be completed on site, including joining and sealing panels, electrical, plumbing and joinery fit off, internal finishes and painting. With a modular approach, all these tasks can be completed off site and the joins between modules finished off on site, maximising the potential benefits of the manufactured approach.
Think Like a Manufacturer and Build Like a Manufacturer
Modular building does have considerable potential to deliver all the benefits claimed of it. By leveraging the benefits of a manufacturing approach buildings can be constructed at high volumes, low cost and in lead times on site builders could only dream of.
However too many modular builders currently “think like builders”. As a result, they struggle with non-standard designs, build inefficiently using a “static build” approach (often outside), struggle with long lead times, too many buildings in work in progress and high working capital.
They suffer high levels of non-value-added time, are constantly disrupted by supply issues and rely heavily on unreliable contract labour. As a result, these builders squander the competitive advantages of manufactured buildings and are left with the disadvantage – buildings that need to be transported to the client site.
Increasingly the best modular builders are “thinking like manufacturers”. Creating standardised and modularised designs, assembling on “production lines” and employing stable efficient “manufacturing” workforces.
At TXM we have helped modular builders become more efficient on four continents. Talk to us about how we can put the “manufacturing” in your manufactured building business.