Applying these 10 Lean layout principles developing a new facility layout can lock in lower costs, shorter lead time and floor space savings. As well, comparing your existing layout to these Lean layout principles can identify the best opportunities to improve your existing layout. Below are ten key Lean plant layout principles and ten simple questions that you can ask to see whether your layout follows the Lean layout principles.
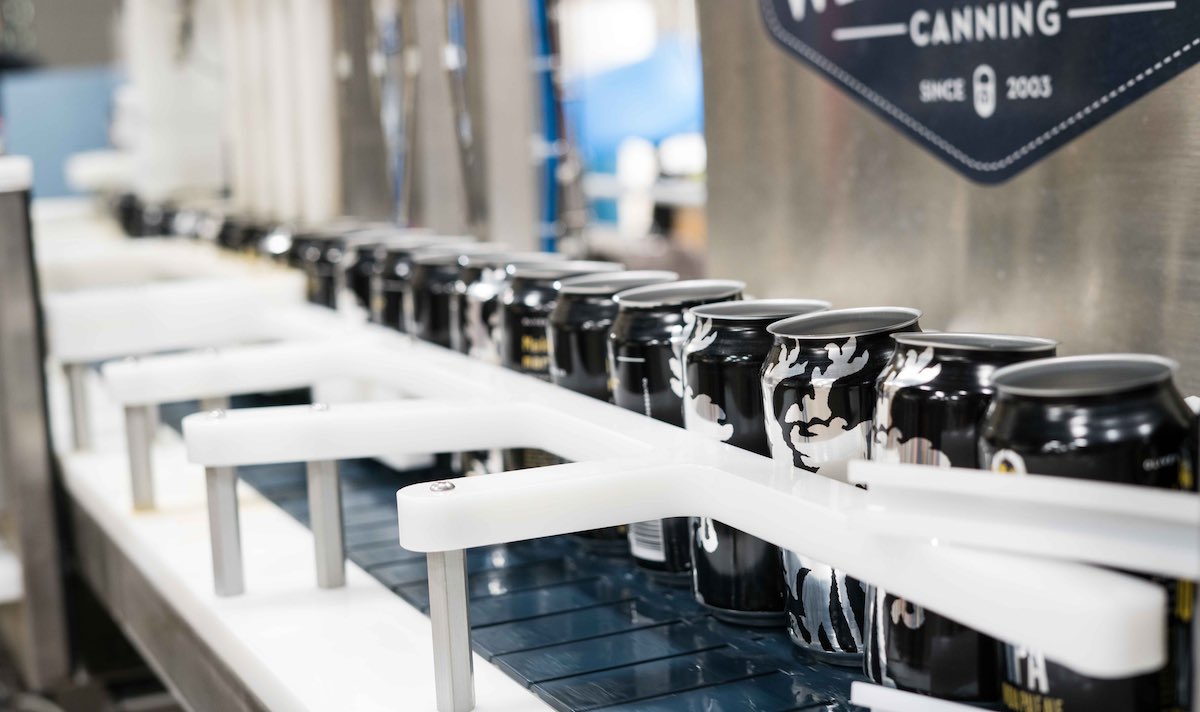
-
The plant operates with One Piece Flow
How often does work flow directly from one process to the next one piece at a time? Are there inventory buffers between each process?
-
There are no process reversals
Do your key processes reverse back on themselves?
-
There are systems and standard work in place to prevent parts shortages
How do you prevent parts shortages?
-
There are no rubbish containers on the shop floor as packaging materials and waste are not delivered to the shop floor
How do you handle the packaging materials that are delivered with your raw materials?
-
The plant features a moving line which is used as a pace-maker for the process
Does your factory have a moving production line that sets the pace of production?
The traditional process-based layout (grey) vs Lean Value Stream-Focused Layout (green)
-
Value Stream Maps exist for key product streams, considering material and information flow, and future state maps are in the process of being implemented
How have you analysed the material and information flows in your process?
-
There are no pits and no platforms on the shop floor
Do your production area feature pits, platforms, and mezzanine floors or is all production work at one level?
-
There are no multiple person processes
Do some of your processes require two or more people working in parallel to complete them?
-
All tools and parts are stored less than 1.5 meters (5 feet) in height, and all work is in the ergonomic strike zone.
Are all tools and materials used by your operators stored at a height of fewer than 1.5 meters? Have you ensured all work is completed in the ergonomic strike zone?
-
Sub-assembly lines are used as required to reduce the length of main lines.
What are the key steps involved in the assembly of your product? Do you have sub-assemblies or is everything assembled on the production line?
As you can see there are a multitude of principles to take into consideration before starting on your Lean Facility Layout. If you need help with your facility, TXM can help you get it right!