Is 5S Really Just a Waste of Time? by Tim McLean
5S is perhaps the most well-known Lean methodology. It is so ubiquitous that some people even think that Lean is 5S. However, many Lean experts are dismissive of the importance placed on 5S relative to other elements of Lean manufacturing. So, is 5S really just superficial window dressing, or is it more than that?
What is 5S?
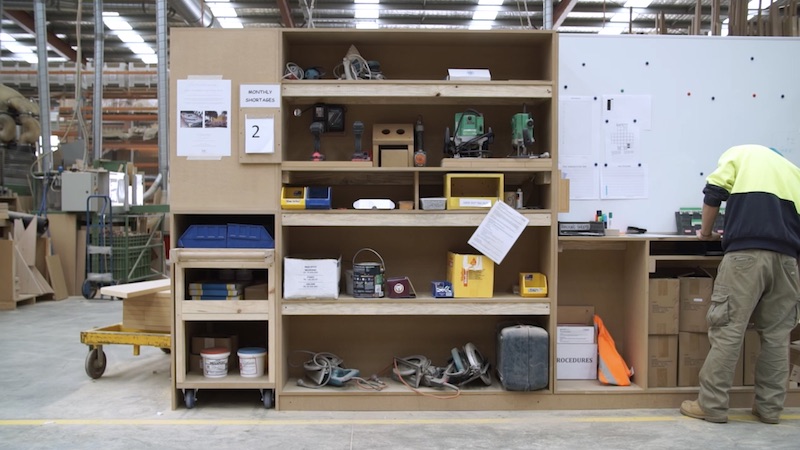
5S is a highly effective approach for organising, standardising the workplace and maintaining good housekeeping. At Toyota the method was originally called 4S, but when it was introduced to the world by engineer Hiroyuki Hirano in his book “5 Pillars of the Visual Workplace”, he adopted the 5S name and this is what has been adopted worldwide. 5S stands for five Japanese words translated into English that represent the five steps of organising and standardising a workplace.
- Sort – sorting the items in a workplace and removing unnecessary items.
- Set in Order – putting all the items in the best location in the workplace for their ease of access and use.
- Shine – cleaning and inspecting the workplace and equipment.
- Standardise – establishing procedures and standards to ensure the first three “S’s” are maintained.
- Sustain – ensuring the 5S process is followed and improved.
Why Do Some People Think 5S is Window Dressing?
5S is a very simple and effective tool and can deliver spectacular visual improvements to a workplace. Dirty, disordered and unsafe workplaces are turned in to shining showpieces where you can (metaphorically) “eat your lunch off the floor”. In a 5S system items in the workplace are located using visual controls such as line marking, signs and shadow boards. Transforming the workplace in this way usually provides a boost to productivity and morale.
However, some people simply take 5S too far. Often so much energy is put in to 5S that it becomes the whole improvement focus of the business. As a result, the business’ lean transformation never gets beyond 5S. In some extreme cases 5S ends up becoming a corporate obsessive-compulsive behaviour with extreme rules such as no personal items on desks and useful items actually banished from the workplace in the name of “eliminating clutter”. It is in this environment some people dismiss 5S as just “cleaning up” and a generator of “non value adding activity”.
As a result of this “bad reputation” 5S often gets overlooked or given cursory consideration in Lean implementations. This is a mistake as 5S is a vital foundation of a successful and sustainable Lean transformation.
No Standard Workplace, No Standard Work
As any self-respecting Lean expert will tell you, standardising the way that work is done is the starting point for improvement. Before you improve any process, you must have a standard, otherwise how can you measure the improvement? Lean standardised work means that each task is defined in terms of the content of the task (the steps involved), the sequence in which those tasks are performed, the time it should take to complete the task and the outcome that will be achieved.
Achieving standard work is not possible if the tools, materials and information that the operator needs are in a different place and presented in a different way every time they go to perform the task. Therefore, to achieve and sustain standard work, the workplace must be standardised. This is where the “set in order” step in 5S comes in, determining the best location for regularly used tools and materials to ensure that they can be easily accessed.
Beyond the practical need of a standardised workplace to achieve standard work, 5S can also help overcome cultural barriers to standard work. In many cultures (including Australia) timing and standardising work can be viewed as dehumanising and strongly resisted by employees. This is particularly the case when these “labour standards” are driven top down by engineers. However, by first implementing 5S, employees are engaged in a discussion about the best way to organise their own workplace. This is empowering for these staff and then makes them more open to a two-way discussion about how tasks can be standardised and improved.
Organising your own “Office”
Managers, administrative and professional staff in a business usually get the chance to decide how their own workstation or office will be arranged. Where their stationery goes, how the computer is arranges and, often, what furniture they have. However front-line employees in a factory, warehouse, maintenance workshop or a farm often get told where things go. When I was an Operations Manager, I usually started a new role by spending a week working alongside front line employees in order to understand how work was done and the challenges they faced.
Often, they would spend hours of their day searching for tools, material and information or walking back and forth to remote stores in order to get the things they needed to do their job. This was intensely frustrating as well as a massive waste of time and resources. In many cases the employees had put up with this for decades as they had never been permitted to change how the workplace was arranged.
With the 5S sorting step, front line staff should be given the opportunity to decide what they need in their work area and what they don’t need. Once that is complete, they decide where the things they need should go and how they should be stored and controlled. It is even better if the front-line teams can get hands-on painting the lines and making up signs and shadow boards for their own work area.
Often the 5S process is the first time front-line teams have ever been asked for their opinion on anything. By rearranging their work area, they take ownership of their work area and, by extension, ownership for the work they do in that area. Engaging team members in improvement is then much easier once they have seen that management will support them to improve their own workspace using 5S. A clean efficient, well organised workplace is also much easier to work in and soon becomes a source of considerable pride in the team.
Unfortunately, some businesses treat 5S as a top down exercise. Centrally developed standards are imposed across the facility and the focus is on enforcement of these standards. This approach tends to disengage and disempower front line teams – the opposite of what is achieved through the bottom up approach described above.
Shine – the Basis of Machine Care
The first time I was involved in implementing 5S was in a plastic packaging plant I managed in the 1990s. When we started cleaning our blow moulders and injection moulders we found problems everywhere. These included leaking hydraulics, compressed air leaks, loose bolts, cracked guards, destroyed conveyor bearings and “cardboard and sticky tape engineering” used to guide the product along bent and damaged conveyors.
The 5S “shine” step often brings the condition of equipment in to focus. By highlighting and fixing all the small visible problems found on equipment, significant improvements in equipment performance and operating costs can be achieved. However, beyond the step change achieved through focused improvement when 5S is first implemented, “shine” can create another cultural shift. Once operators have found the problems on their machines and seen these problems fixed, ongoing cleaning becomes inspection. The teams are trained to look for problems and soon can take on some maintenance tasks of their own such as tightening loose fasteners, belts and chains and lubricating bearings. This is called autonomous maintenance and along with focused improvement often prompted by the initial shine, is one of the pillars of Total Productive Maintenance.
Sustaining and Improving
The fifth “S” stands for “Sustain”, or as we prefer to say at TXM “Sustain and Improve”. For many this means 5S audits. Unfortunately, this is an area where most 5S deployments fail. A perfectionist approach is taken to audits and many have the view that audits need to be “independent”. Audit checklists are complex and lengthy and the “independent auditors” rarely have time to complete their audits. In any case they are auditing someone else’s workplace so their interest and investment in the audit process is going to be limited.
As well “independent” auditors provide a catalyst for tension and conflict between teams if the team being audited feels they have been treated unfairly. Thinking about it, after empowering teams to improve their own workspace through 5S, there could be no more effective way to destroy this empowerment by getting a manager or supervisor from another area to come and tell the team that their work is not up to standard. Most people will try and avoid this conflict, so pretty soon the audits become meaningless and then don’t happen at all. After that the team takes the message that 5S is no longer important and the system gradually falls away.
At TXM we believe that each front-line leader should audit their own area. We use a simple, highly visual weekly audit and results of the audit are displayed on a 5S visual management board in the work area. The skeptics among you will suggest that a leader auditing his own area will only give himself a great score. To overcome this, we ensure that photographic visual standards are displayed at each location in the workplace showing what that workplace should look like. The role of the manager is then to notice when the state of the workplace deviates from the standard (and the audit) and ask why. The manager can then coach their front-line leader on what is expected and how to achieve it.
Rather than intimidating and demotivating the front-line leaders, this coaching approach shows the front-line leader that the manager is interested in their area and their work. By asking “why” rather than just condemning the state of the workplace and directing the front-line leader to “clean up” the manager can also uncover problems that the team may be unable to solve themselves. For example, staff from another area may be dropping materials or waste into the team’s work area (perhaps because they have nowhere else to put it) or a poorly maintained machine might be creating excessive dust. Engaging in the 5S discussion helps identify and solve problems that go well beyond the housekeeping and organisation of the workplace. Further, measuring and improving 5S performance provides a starting point for measuring and performing other areas of the team’s performance.
Not a Waste of Time, But Not the Answer to Everything
To conclude, 5S is definitely not window dressing, but instead an essential foundation of a successful Lean manufacturing implementation. However, while a house will not stand for long without good foundations, likewise there is much more to a house than its foundations. Businesses that stop at 5S really miss seeing the whole picture of what Lean thinking can deliver.
Implemented well, 5S is a tremendous tool to engage the whole workforce in improvement. It is a vital prerequisite for implementing standardised work and Total Productive Maintenance and a great way to engage teams in visual management. For managers, it requires a focus on noticing and acting on deviations from standard, asking why and coaching improvement.
At TXM, almost every Lean implementation project we conduct will include implementation of our Practical 5S® (P5S®) approach. However, our approach is to implement P5S® in parallel with making improvements to the value stream, rather than waiting for 5S to perfect before making more fundamental process change.